8 steps to producing more in less time: Production efficiency
During this article, we explain how to boost production efficiency with eight actionable steps, helping you achieve more in less time.
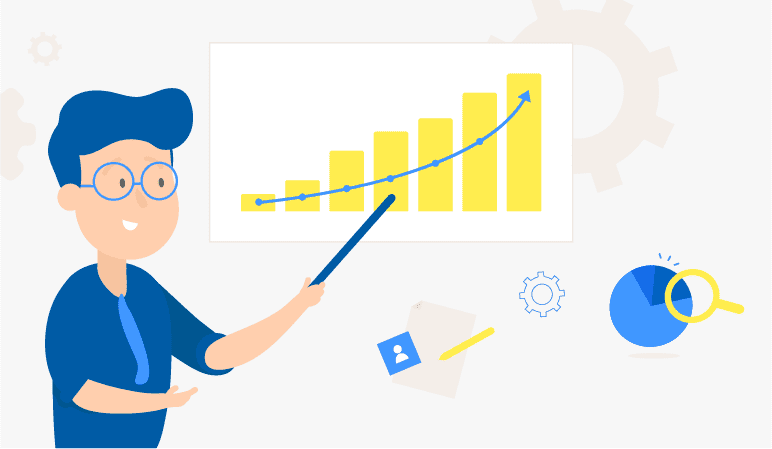
Efficiency is at the top of most companies’ wish lists. When applied to manufacturing, this implies you’re producing the maximum possible in a minimum of time. And this is where the term production efficiency comes into play.
But what is ‘production efficiency’ exactly?Copied
‘Production efficiency’ primarily relates to the time one or more items of machinery are operational. 100% production efficiency means all machinery and/or operations are running at maximum capacity.
In other words, it wouldn’t be possible to produce even a single additional item without:
- sacrificing production of some other item
- improving production technology
How does this benefit you?Copied
From a financial perspective, the foremost benefits of production efficiency include:
- improved quality
- greater revenue
- higher productivity
Optimal production efficiency also means that you’re manufacturing your goods at the lowest possible cost price. In addition, production efficiency goes hand in hand with minimal resource wastage – time, money, energy, raw materials. Often, the term is also used as part of the lean philosophy, which emphasizes continuous improvement of processes and value creation.
Calculating efficiencyCopied
To boost your production efficiency to the highest level possible, it’s worth making the term as tangible as possible. Fortunately, there’s an easy way to calculate production efficiency.
Simply divide actual production line output by the maximum (standard) output rate feasible for a given time window, assuming you’re using a standard method. Then multiply by 100 and express your answer as a percentage.
Efficiency (%) = output ratio ÷ standard output ratio ×100
A step-by-step plan to higher production efficiencyCopied
But how should you go about improving your company’s production efficiency? Here’s how!
1. Improve your operational processes
It doesn’t matter if you’re at the helm of a small, family-owned business or a multinational manufacturing conglomerate – every type of organization has a natural tendency to fall back on deeply entrenched habits. Often, you’ll hear, “But this is how we’ve always done it,” anytime someone suggests changing the way you do something.
Sadly, stagnation often means decline. Many companies invest tonnes of money in new machinery and other operating assets, but hold on to antiquated operational processes and procedures. Having state-of-the-art machinery is all well and good, and looks great too, but doesn’t automatically result in spectacularly higher output if your underlying support and administrative processes date back to the Industrial Revolution.
So, take the time and make the effort to critically examine your operational processes. Don’t be afraid to rock the boat by pulling your procedures into the modern age. Constant change is paradoxically the only thing that never changes.
Read our article, 6 ways to streamline your existing operational processes.
2. Evaluate your production line performance
The production line lies at the heart of any manufacturing company. By carefully examining each manufacturing facility and its daily capacity/output, you can map how your production line(s) are performing. It also gives you insights into the costs you incur anytime a line comes to a standstill or isn’t running at maximum capacity.
3. Update your technologies
Technology is inescapable in the modern-day manufacturing landscape. Companies that fail to digitalize their operations will sooner or later price themselves out of the market. So, look very carefully at both the hardware and software technology you’re using.
If you’re still using old computers that take five minutes to boot up and load in your business-critical control programs, then you’re wasting time – day in, day out – before the information reaches your production line. You might say, “Five minutes isn’t very much.” But annually this is over twenty hours’ delay per production line or worker.
4. Identify your bottlenecks
Bottlenecks arise wherever one or more defects exist in your production process. We’re inclined to look solely at machinery and equipment for bottlenecks, but in reality the human factor is often what undermines production efficiency.
Administrative errors that prolong turnaround times are a prime example, but a lack of preventive maintenance is also a common source of bottlenecks. So, identify any actual or potential bottlenecks in order to maintain your production process efficiency.
5. Eliminate waste
Waste is the biggest source of inefficiency. Some forms of waste, such as defective machinery and/or waste materials, are self-evident and easy to solve. But there are other sources that are less discernible or tangible. Examples include substandard HVAC systems. Day in, day out, you’re wasting costly energy. It’s not immediately obvious, but over time this leads to huge expenses and harm to the environment.
Other forms of energy wastage include mismanagement and poor work planning because you’re wasting your employees’ energy – yet another form of capital destruction. What’s more, inefficient working processes also lead to a fair degree of frustration in the workplace. So, look critically at the way you use power and human resources within your organization.
6. Get organized
Disorganized teams often work inefficiently. Organize and standardize as many processes as possible across the board. The best way to do this is to streamline communication between employees and departments.
If your staff have to scroll through screen after screen of SMSs, emails, or apps, or wade through reams of hard-copy memos before they can start work, then production efficiency is going to suffer. Appoint single points of contact to coordinate information flows.
Standardizing work processes also ensures that your staff know exactly what is expected of them.
7. Improve your training programs
Your staff are generally the net result of your company’s culture. If they’re not working efficiently, then it’s probably because they’re following a bad example.
Fortunately, this is easy to solve by offering your staff relevant training programs. Emphasize standard operating procedures and make sure all your learning resources and programs are readily accessible. Examples include good software tools, instructional videos, and on‑the‑job training.
Make sure that your employees keep up to date and move with the times.
Tips!Copied
Putting the steps outlined above into practice will get you a long way toward making significant efficiency improvements. Below, you’ll find four valuable tips to give your production efficiency a boost.
1. Standardize repetitive processes
In the manufacturing sector, you can make major strides by standardizing your processes, especially where many are highly repetitive. Create a checklist and protocol to steer your standardization efforts in the right direction.
2. Prevent problems before they arise
We’ve all heard the saying, “Prevention is better than cure,” and this certainly applies to production efficiency. Within manufacturing, this relates primarily to preventive maintenance of your machinery and ancillary equipment, saving you lots of money in the longer term.
3. Encourage cooperation
Sharing a common goal and working toward this goal together is the best way to unite productivity and efficiency. Don’t be afraid to embrace modern mobile technologies, as these can foster and nurture collaboration, for example video conferencing and workflow automation.
4. Visualize your employees’ skills
Efficiency requires having a good overview. And this, in turn, entails knowing exactly who has mastered which skills and competences, and who hasn’t. Skills matrices are the ideal way to help you visualize this information.
Using skills matrices provides numerous benefits.
- They greatly simplify work planning. Suppose one or more staff members are away or you’re heading into a peak period – you can see at a glance who to deploy and where. This can only serve to boost your efficiency.
- Skills matrices are also a great means for mapping and tracking team and/or individual progress.
- As you can see, they’re flexible and versatile tools. Both management and staff can use them for general planning purposes, but also for very specific objectives.
AG5’s software is ideal for creating and maintaining clear, concise skills matrices and works far better than spreadsheets. Find out what AG5 can do for you and schedule a demo to satisfy your curiosity!