What are the pros and cons of standardizing operational processes?
During this article, we explore the advantages and disadvantages of standardizing operational processes, offering insights into how this practice can enhance efficiency while considering potential drawbacks and challenges.
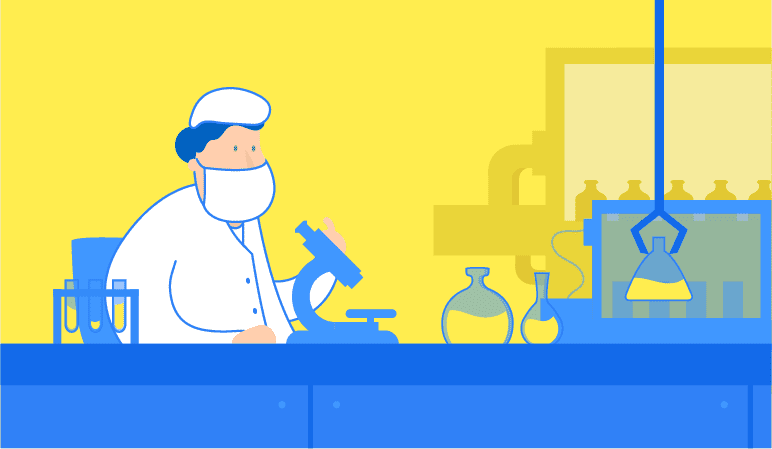
Standardizing operational processes is vital to organizations looking to achieve consistently high quality levels. Yet it’s not a priority on every company’s agenda. A missed opportunity – it could be the key to your success!
But what do we mean exactly by standardizing operational processes?Copied
This article primarily examines standardization within the manufacturing industry because it’s here that we see the biggest benefits due to the scale and repetitive nature of its operational processes.
Standardization in this setting involves applying or adhering to an internal or external standard whenever designing, testing, or configuring a certain process.
In essence, this boils down to creating a set of rules or best practices for each operational process, for example a set sequence in which you perform certain tasks or safety procedures to be followed by staff at all times.
You can apply principles of standardization to virtually every operating process, be it how to handle telephone calls, comply with safety standards, or assemble, package and dispatch a product.
Internal audits are a good way to test whether standardization works well in practice. If you’re applying external standards, an external certification agency or standards institute might conduct external audits to determine whether your organization complies with its certification standards.
The prosCopied
Standardizing operational processes provides many interesting benefits, for example:
1. Clarity
Complex processes often comprise elements that are open to differing interpretation. Standardization provides a clear set of detailed instructions for performing each operating process. This ensures a uniform way of working that is clear to all staff in question.
2. Measurability
Standardization allows you to measure results and determine your efficiency and productivity.
3. Quality
Standardizing operating procedures for marketing, manufacturing, or sales clarifies the results for each stage of the process. Ultimately, this sets a universal standard that ensures consistently high quality levels. This is great for your reputation, improves your service standards, and creates greater customer loyalty.
4. Repeatability & error susceptibility
If you’ve configured a process according to basic principles and best practices, it’s theoretically possible to repeat the process ad infinitum and to a consistently high quality level. Doing so also makes operational processes less susceptible to human error.
5. Portability & transferability
Well-defined standards can help new hires get to grips with their new role more quickly and help them become fully fledged productive team members in no time. What’s more, standardization also helps experienced co-workers transfer their knowledge to new employees more easily and rapidly.
6. Innovation & automation
If you already know how a process works in minute detail, it becomes a lot easier to innovate and automate. In turn, you’ll be able to implement improvements more quickly and effectively, while gaining keener insights into the elements you can automate. What’s more, automating repetitive tasks allows you to perform certain operations faster and more cost-effectively.
7. Productivity
Suppose there are three ways to perform a certain task within your organization. This will undoubtedly lead to situations in which the way your employees work will lead to some form of conflict. Standardization ensures uniformity throughout your organization so that teams and departments can work with one another more easily, generating synergy and leading to higher productivity.
8. Job satisfaction
Applying high quality standards to operational processes can give workers a sense of ownership over their work. The feeling that their work is useful and meaningful generally results in higher job satisfaction levels.
The consCopied
As with many other things, standardization also has its cons. Avoid some of the following pitfalls if you’re looking to make the most of standardization.
1. Reduced creativity
Standardizing operating processes can sometimes smother creativity and innovation because it involves setting methods in stone from which your staff aren’t allowed to stray. Diversity and creativity are forced into a straightjacket.
You can avoid this pitfall by explaining the aim of standardization in detail. Standardization isn’t about stifling creativity or dismissing promising ideas. Instead, it’s about eliminating inefficiency and ineffective operations.
So, listen carefully to employees who have good suggestions about how to improve standard operating procedures still further. And take action or follow up on these suggestions. After all, ‘standardized’ doesn’t mean etched in stone until the end of days! New insights and improvements are also part of the standardization process.
2. Too many concessions
It’s generally the operators on the work floor who are ultimately responsible for implementing standard operating procedures. However, many managers are often inclined to make too many concessions.
Although it’s important to listen to your operators’ needs and requirements, making too many concessions can undermine the effect and efficiency of your standardization efforts.
3. Data fragmentation
It’s virtually impossible to standardize your processes without solid data. A potential pitfall when collecting and using data is that key information is too fragmented, for example it’s kept in separate silos and isn’t readily accessible. Successful standardization relies heavily on how well you’ve structured your data.
Tip – make it visual!Copied
Once you’ve standardized your processes, you’ll know who can do what, and everyone will know how. But to capitalize on this, for example being able to find replacements fast, identify your most highly skilled personnel, and put together the most versatile project teams possible, you’ll need to keep track of all your skills and competences. There’s no better way to do this than to use skills matrices or skills management software. AG5’s software can help.
Schedule a live demo to learn about AG5’s benefits or download our Excel spreadsheet templates to experiment with your own skills matrices.
Use AG5 to identify skill gaps
Say goodbye to Excel matrices. Start using AG5’s plug and play skill matrix software.
ISO27001 certified
Start your 14-day free trial