How continuous improvement and skills management go hand in hand
We explore the integration of continuous improvement practices with skills management in this article, highlighting their synergies and benefits for organizational and employee growth.
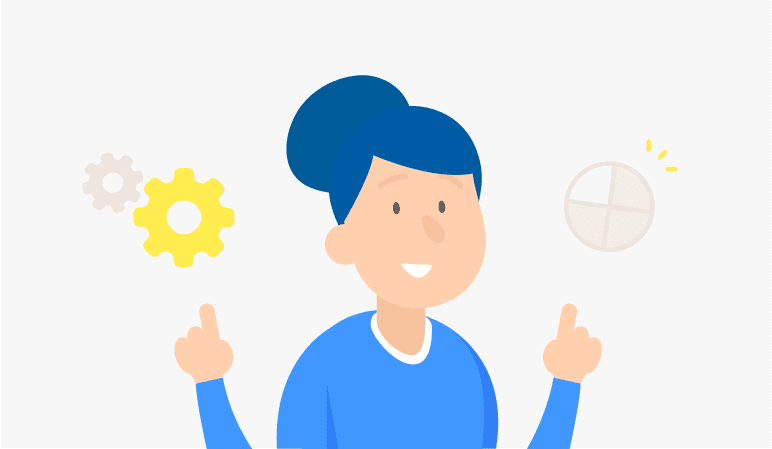
Your organization’s success is largely dependent on your employees’ skills and competences. Skills management and continuous improvement allow you to map skills and competences, and then plan and develop them further.
But how should you tackle strategies such as continuous improvement and skills management in practice? And how do they complement each other? Find out how!
Why adopt continuous improvement?Copied
Continuous improvement has almost become a standard slogan in today’s business world in which market demand and requirements are changing by the day. It’s key for companies looking to remain competitive in the longer term.
But what is continuous improvement?
Continuous improvement – also known as Lean and Kaizen – is an ongoing effort to improve products, services, or processes by means of ‘incremental’ improvements over time. It also addresses issues such as cost reduction.
A characteristic of this way of working is that it doesn’t involve one-off measures, but continuous improvements as a gradual, never-ending change – or more simply ‘getting better all the time’. What’s more, these improvements are put forward and carried out by the employees themselves.
3 steps to continuous improvement
Continuous improvement can be split into several pre-defined phases. Read about these phases below.
- Analyze and generate suggestions for improvement. This first phase involves identifying and classifying any problems. Analyze the facts and then clearly determine your organization’s core values and objectives, and the extent to which these relate to current operational processes. Always keep your customers’ perspective top of mind while doing so. What do your customers want?
Make sure your employees put forward suggestions for improvements as a team to encourage employee engagement. Workshops and brainstorming sessions are also good ways to implement this first phase. - The second phase involves putting into practice the suggestions for improvement that you identified in Phase 1. Again, do this as a team and involve as many stakeholders as possible, for example other departments, suppliers, customers, etc. Experience has shown that diversity often leads to better solutions and wider acceptance.
- The third and final phase involves monitoring and learning. Once you’ve implemented the suggestions, it’s important to measure and monitor their effect. Check that they’ve actually resolved the problems and/or to what extent. Evaluate your solution carefully and use any insights gained as input for your next incremental improvement.
What are the benefits?
But what’s the benefit to your organization from implementing continuous improvement? Once you’ve analyzed your results, you should discover a number of benefits.
- Continuous improvement helps you improve processes. Throughput times are often shorter, costs reduced, and errors minimized.
- By embedding continuous improvement throughout your organization, you’ll also raise customer knowledge levels. When every employee knows what customers want and expect, it’s so much easier to identify the components of processes or customer journeys that need attention. You’ll end up meeting your customers’ needs and requirements far more easily, and even exceeding their expectations.
- Continuous improvement also raises knowledge levels among employees about your organization’s objectives. Terms such as ‘strategy’ and ‘core values’ then take on greater meaning for your entire workforce.
- It also encourages ongoing professional development at individual, team, and leadership levels. Ultimately, your workforce will become far more flexible and dynamic.
- Continuous improvement also leads to greater engagement, reduced absenteeism, and increased job satisfaction.
- In the current economic climate, change is the only constant. Today’s innovations may be totally outdated in six months’ time. Continuous improvement encourages agility and increases adaptability. Vital for any company looking to remain relevant in the future!
Methodologies incorporating continuous improvement
Various methodologies make extensive use of continuous improvement, especially in the manufacturing industry.
Integrated Work System (IWS) is an improvement framework based on total employee ownership. It focuses on making production and fabrication processes more reliable, reducing costs, and increasing productivity. Companies such as Intersnack, Philip Morris, and EY have embraced IWS to optimize their operational processes.
World Class Manufacturing (WCM) is a collective term for three optimization methods – Lean, Total Productive Management (TPM), and Six Sigma.
Training Within Industry (TWI) is a tried‑and‑tested method for training employees quickly and effectively. It was introduced in the United States during the Second World War, and then rolled out worldwide. TWI minimizes onboarding time and error rates, while raising individual, team, and organizational performance levels. Learn more about Training Within Industry.
Enter, skills management softwareCopied
Continuous improvement works best when you combine it with skills management. Skills management simply entails mapping out your organization’s expertise and experience in full. It also involves correlating information with company objectives and market demands.
How does skills management complement continuous improvement?Copied
Managing skills helps make continuous improvement more effective and more manageable.
Greater insight into tasks and requirements
Skills management revolves around visualization of the skills and competences required to perform a certain task. Suppose you need at least three people to perform a specific task and safeguard continuity, for example operating a production line or using a certain software program.
Skills matrices’ visual layout allows you to see at a glance if you’re able to meet this requirement. The results allow you to plan and shape your continuous improvement efforts.
Improved response to absenteeism and peak periods
Every organization has to deal with peak periods or extended employee absenteeism from time to time. Skills management makes it possible to respond more rapidly and effectively. It allows you to guarantee a pool of qualified replacements and improve processes to better deal with peak workloads.
Progress monitoring
Continuous improvement is a long-term, never-ending process. Skills management is an ideal way to monitor the progress you’re making. This increases the effectiveness of your ongoing process improvement efforts.
Wider reach
Skills management offers you so many options. You can implement it at a team, departmental, or even an organizational level. It will ultimately make it possible to create custom solutions that make continuous improvement even easier and more effective.
Key players
Although continuous improvement impacts entire organizations, key players are often instrumental in its preparation and implementation. Once you’ve adopted skills management methods fully, it becomes far easier to identify these individuals. Thanks to tools such as skills matrices, you can see at a glance who has which skills and qualifications.
The benefits of skills management softwareCopied
If you’re looking to get the most out continuous improvement in combination with skills management, then AG5’s software is the perfect tool. Our skills management software allows you to do the following:
- enter updates and training results real time from the shop floor
- link projects to specific expertise and experience
- set notifications for individuals, teams, or qualifications
- simplify finding qualified operators for complex tasks, e.g. retooling production lines
- find the best replacements for employees off sick in a single search
- display skills and competences across multiple company sites
- replicate organizational structures and link employees to qualifications using drag ’n’ drop menus
Using AG5’s software, you circumvent the pitfalls and limitations of spreadsheets. Maintaining skills matrices in Excel is complex, error-prone, and time-consuming
Curious about what AG5 could do for you? Feel free to get in touch or schedule a live demo.