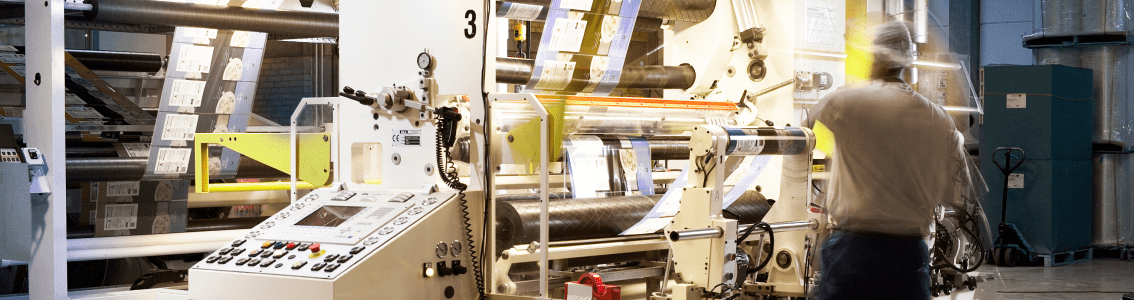
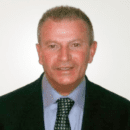
Vista
Vista’s John Kanters was looking for a skills management system to connect employees more closely to the company in the future.
Results achieved:
- Reduction of non processing hours
- No more wasted funds due to overtraining
- Everything in one place, no more separate Excels per department
- Skills gaps are now transparent as are the necessary actions
We needed greater overall clarity. Not just of a single department, but an overview of all departments
What improvements have you seen using AG5 compared to Excel?
We established development roadmaps to show our people how best they can develop from one position to another. So certain training courses are now linked to each individual position. For clarity’s sake: if you wish to develop from Operator A to Operator B, for example, then you must follow the specific training courses. We now have a clear overview of this for each person: how far is an employee along their Development Plan?
We are a typical US company – very data-driven and everything is based on targets. We used to maintain this in Excel, but each department did this separately. Everyone did it in their own way.
We needed greater overall clarity. Not just for a single department, but an overview of all departments We can now see, for example, that we need to train 3 people per shift. We now now who has those skills, and if those skills are missing then we are aware of the skills gap directly. And then you know exactly who to train. We never had that overview before, but thanks to AG5 we now do.
How does AG5 help in forecasting personnel requirements for each production process?
The intention is that, based on the forecast, we will soon see how many people are required per shift for each production process. We can now see which skills have been acquired, but can also see any gaps. And something that we couldn’t see previously was that we are actually overtrained for a number of processes. Those funds were therefore simply wasted in the past and that money could have better been spent differently. Now we can see this clearly in AG5.
If, for instance, you only need 4 people for a given production process but 14 have been trained, then you have spent a lot of money for no good reason. This is expressed here in hours, i.e. non processing hours. As it means that the employees concerned were not productive in that period. If for example you have had 200 non processing hours, and one hour costs 50 euro, then it has unnecessarily cost 10,000 euro.
Tired of managing skills in Excel?
Say goodbye to Excel matrices. Start using AG5’s plug and play skill matrix software.
Recognized by G2 for Excellence in Skills Management
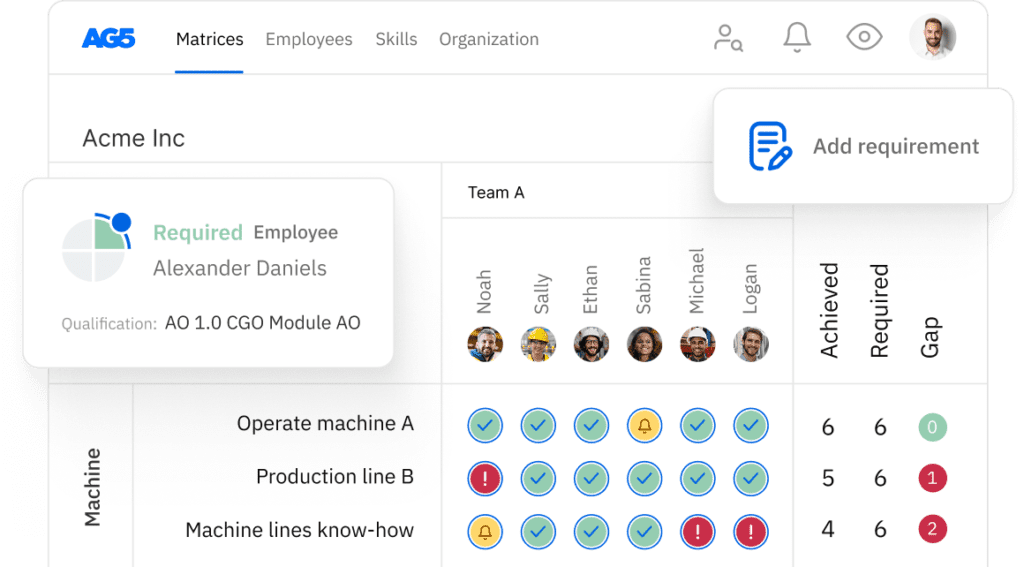