6 ways to streamline your existing operational processes
In this article we talk about six effective strategies to optimize your current operational processes, offering actionable insights to enhance efficiency and productivity across your organization.
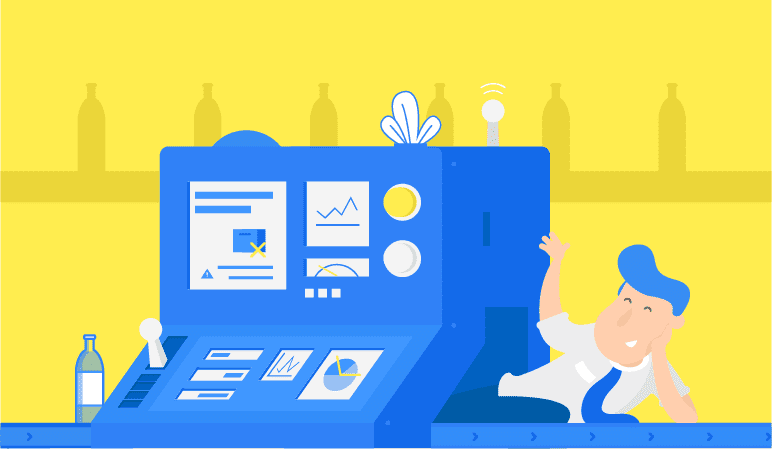
Efficient, streamlined operational processes are key to your organization’s success, which is why it’s worth optimizing and improving them on an ongoing basis. This article discusses how to do just that.
Three types of operational processCopied
Before looking at how to improve your operational processes, it’s important we first define exactly what we mean by an “operational process”. In essence, it’s a set of procedures, agreements, or protocols, which translate to a series of tasks or activities performed by one or more people in a set sequence. The main aim is to manufacture a product or provide a service for your customers.
In practice, there are several types of operational process:
- control processes – policy-related activities, for example planning, control, evaluation, and adjustment
- primary processes – main activity, for example manufacturing products or providing services
- support processes – secondary activities to ensure success, for example safeguarding primary processes and allowing staff to focus on their core tasks
This article focuses on primary and support processes, as these are often where the most gains can be made.
Why even bother optimizing your existing processes?Copied
With the right mindset, approach, and tools, it’s possible to optimize pretty much any operational process. Doing so has a noticeable effect in many areas – benefits include:
- improved quality – meeting your customers’ needs and requirements, exceeding their expectations, retaining them as customers, and increasing your turnover
- shorter turn around times – quicker time to market for products and/or services
- reduced costs – eliminating material waste and unnecessary steps
Improving your existing operational processesCopied
The right approach depends largely on the type of process and the context within your organization. Here are a few options:
1. Find and eliminate “waste”
It’s not always immediately obvious, but certain processing stages or tasks are often partially or wholly redundant. An example might be a standard letter that is forwarded to six or seven people for sign-off without anyone changing anything significantly in terms of content or tone. Or certain tasks that you really only need to carry out once, but repeat at several stages throughout the process.
Finding and eliminating these unnecessary operations is the first step toward higher operating efficiency.
But how do you work out whether a processing stage is a waste of time and resources, or not? Ask yourself the question, does a processing stage or series of operations actually add any value to your product or service? If not, you’ve probably found yourself an example of waste or an unnecessary operation.
2. Optimize your production process
Manufacturing is a single multifaceted operational process in its own right. Improving your production processes often allows you to make a huge leap forward in terms of overall process optimization.
Ways to improve your production processes include:
- closely examining current workflows
- regularly updating processes and technologies
- carefully planning scheduled maintenance work
- investing in staff (training courses, workshops, refreshers) and workplace (neat, tidy, safe)
Don’t miss out on other great tips in our article, 10 ways to improve your production processes.
3. Stick to deadlines
Confusion about deadlines, tasks, and roles within an organization is often the bottleneck that hamstrings your operational processes. Setting clear and attainable deadlines is therefore critical to your optimization efforts, and has many benefits:
- clarity – a win-win for all: co-workers, suppliers, customers
- shared goals – a target for everyone to aim at as a team
- motivation – an impetus to strive for higher performance levels
But make sure you set deadlines that are reasonable and attainable. And not every step or stage needs to be subject to a tight deadline, as this constricts workflows unnecessarily and becomes stressful.
4. Find replacements fast
Manufacturing companies often fall victim to production line downtime or standstills because a key employee is away or off sick. Finding a suitable replacement quickly is vital to safeguarding operational continuity.
Manually flipping through sheet after sheet of an Excel skills matrix is tantamount to searching for a needle in a haystack. And that’s assuming your spreadsheets are even up to date!
A better way to deal with this eventuality is to use skills management software. Type in the required qualification and, hey presto, out rolls a list of suitable replacements.
Watch our explainer video to see how this works:
5. Introduce on-the-job training
Lifelong learning is vital to keeping ahead in today’s labor market. On‑the‑job training is a great way to achieve just this, as it embeds learning into daily work routines in an intensive and practical fashion. Learning materials also form an important part of employees’ daily work.
Its main aim is to help employees make as much progress as possible in the shortest time possible and has many advantages over traditional learning methods because staff:
- put theory into practice as quickly as possible
- receive immediate feedback in the workplace
- don’t have to take time off work, cutting costs and boosting productivity
On-the-job training makes it possible to immediately evaluate training results in the workplace. This, in turn, allows you to determine which aspects of your training program work well and whether they meet your staff’s professional needs and requirements.
Don’t miss out on other great tips in our article, What is “on‑the‑job training” exactly and why is it so effective?
6. Improve onboarding procedures
Onboarding your new hires is an important part of recruitment and talent management that is often overlooked, yet it has many benefits:
- Staff who’ve received a thorough onboarding are more productive more quickly because they learn the relevant knowledge and skills for their new role early on.
- It also means that new hires get better acquainted with the company culture sooner.
- This results in a better “click” with the rest of their team.
- Oftentimes, new hires leave prematurely because their onboarding is chaotic, incomplete, or simply unpleasant. This is pretty detrimental for your staff turnover!
- Providing new hires with a thorough onboarding also serves as highly effective word-of-mouth advertising.
Don’t miss out on other great tips in our article, 12 tips for onboarding new staff as effectively and efficiently as possible.
Conclusion – continuous improvementCopied
A strong organization relies on smooth, efficient operational processes. This article’s tips will help you make headway with your optimization efforts. And last, but by no means least, don’t forget to keep track of your workforce’s skills, qualifications, and certification.
An ideal tool to achieve this is AG5’s skills management software, which allows you to paint a complete picture for each employee. What’s more, you can access and update this information from the work floor – anytime, anyplace, anywhere.
Schedule a demo to find out how to get to grips with skills management.