10 ways to improve your production processes
In this article, we’ll offer tips, tricks, and strategies on how you can improve your production process, and how you can implement this approach.
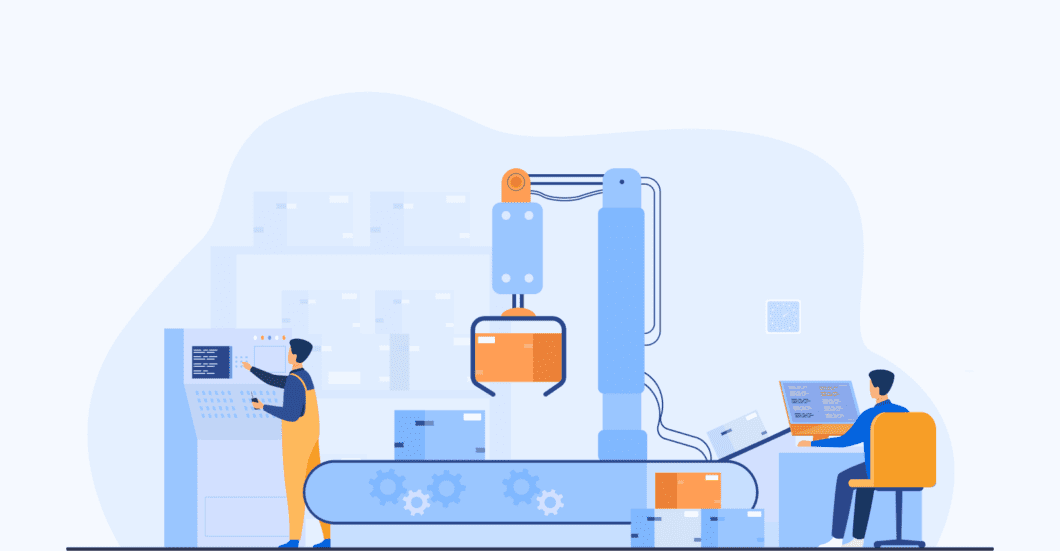
In manufacturing, streamlined production processes are crucial for success. They help businesses operate more efficiently, effectively, and safely.
To optimize your production processes, however, you’ll need a comprehensive approach toward your employees, machines and tools, and technology that allows you to track and manage the skills, certifications, and qualifications necessary for business operations.
In this article, we’ll offer tips, tricks, and strategies you can use to develop and implement this approach. We’ll also take a look at the ways in which AG5’s skills management software can help you improve your production processes.
The benefits of improving your production processesCopied
Before we dive in, we’ll take a closer look at the importance of optimizing your production processes through the lens of the benefits that doing so can bring your organization.
- Higher productivity. By analyzing your processes regularly and thoroughly, you’ll learn to spot and resolve inefficiencies and bottlenecks more quickly – as well as predict future problems – and streamline workflows
- Faster time to market. By working more efficiently, you’ll be able to put out a higher-quality product faster than before
- Improved product quality. Thorough testing also has repercussions for other key product characteristics, such as performance, life span, user-friendliness, and safety
- Higher rates of customer satisfaction and loyalty. Because you are putting out a higher-quality product, your customers will be more likely to become repeat customers, leading to a competitive advantage
Pitfalls to avoid when improving your production processesCopied
Let’s also take a brief look at several pitfalls we often see clients in the manufacturing industry face when improving their productions processes, as well as steps you can take to avoid them.
Lack of clear objectives. Ambiguity can lead to misalignment among your workforce, as well as wasted resources. Set clear and specific objectives for any improvements you want to implement to ensure that everyone is working toward the same goal
Overlooking change management. Improving production processes often requires changes in workflow, responsibilities, and culture. You should take steps to ensure that your employees understand and support the changes you’re implementing to avoid resistance and pushback
Focusing solely on short-term goals. While it’s important to achieve quick wins, focusing solely on short-term gains may lead to neglecting the long-term sustainability and scalability of your new production processes
6 tips for improving your production processesCopied
You can use the following tips to directly improve your production processes.
1. Analyze your current workflows
You can only go from A to B if you know where A is. With this in mind, take a close look at your workflows from three perspectives.
- Personnel. Are the right people with the right skills in the right place at the right time? Have you clearly defined objectives for your production processes that are SMART (Specific, Measurable, Assignable, Realistic, Time-related)?
- Processes. When did you last map and evaluate your processes? Where are potential bottlenecks and obstacles?
- Tools & technology. Is your machinery and equipment in good condition? Are you using the most efficient technology? How easily can you alter your production processes?
2. Modernize your processes and technologies
Once you’ve mapped your current workflows, you can begin to determine whether you should modernize or improve your processes and technologies.
- Can you automate certain processes?
- Use software to improve planning, inventory control, or monitoring?
- Replace or upgrade your equipment and machinery?
Tip: Be sure to estimate the “total cost of ownership (TCO)” [1] of any new technology or equipment you plan to use. TCO includes the cost of purchasing, implementing, using, and retiring equipment, machinery, tools, software, or other assets used in your manufacturing operations.
3. Pay attention to planned maintenance
One of the main causes of inefficient production processes is a lack of planned maintenance. Broken or worn-down machinery costs far more to repair than routine maintenance.
Consider the following:
- Train operators and maintenance technicians so they can respond quickly and effectively when a problem arises with equipment or machinery
- Set fixed dates and times at regular intervals for your planned maintenance
- Consult with employees who work on the shop floor to determine the best times to schedule your planned maintenance
Tip: Read our article, “So, what is TPM?” to learn about “total productive maintenance” – a method of planned maintenance that can help your organization avoid costly downtime stemming from equipment or machinery that needs repair. [2]
4. Develop targeted training plans for employees
The more effectively and efficiently your employees can operate and maintain your machinery and equipment, the less the risk of costly downtime.
Your employees should be able to learn new skills, attend training, and earn certifications they may need for their roles. To enable this, you’ll need to track and manage the skills, qualifications, and certifications your employees have – as well as those they need.
5. Keep your workplace clean and organized
An organized workplace is a precondition for optimized production processes – and perhaps the most important aspect of overall workplace safety.
Create an efficient layout for workstations; organize, sort, and label hand tools so they are easy to find; try to minimize the distance between tooling and machinery – anything that makes the workplace easier and safer to navigate!
6. Strike a balance with inventory
Make sure you know exactly what you have in stock and where it is – and take strides to ensure that you are never overstocked nor at risk of stockouts.
Use software to track inventory levels, predict material requirements, and receive automatic notifications to ensure you strike a balance between too much and too little.
4 examples of optimization strategies for your production processesCopied
The remainder of our 10 ways to improve production processes will focus on strategies you can implement in your organization that will help ensure your operations are running as smoothly as possible
Continuous improvement
Continuous improvement is one of the pillars of the Lean method [3]. By continuously improving, organizations are taking steps to boost productivity, quality, costs, and turnaround times gradually and iteratively, rather than as a one-time, large-scale transformation.
Continuous improvement implies that optimizing production processes is a neverending endeavor, and relies on employees to make changes and improvements, This is why it’s important to provide on‑the‑job training and coaching, so your employees can develop along with your production processes.
Continuous improvement comprises three main phases:
- Gather suggestions. Identify and summarize the problem or issue
- Implement feedback. Resolve those problems using suggestions, feedback, or ideas you’ve gathered
- Monitor and learn. Evaluate the efficacy of the resolutions you have implemented
Performance Support
Performance Support is a method for improving production processes based on practical learning. [4] It involves creating “learning moments” tailored to employees’ practical requirements.
Performance Support comprises five “moments of need”
- New. A need to learn something new or acquire new skills
- More. A need to learn more about a specific topic or way of working
- Practice. A need to put certain information, skills, or procedures into practice
- Change. A need to keep abreast of change(s)
- Solve. A need to overcome and solve problems
Workforce planning
Workforce planning aligns an organization’s priorities and requirements to those of its available employees. It primarily addresses factors such as:
- Scope. Do you currently have a lot of job openings?
- Mix. Do you have the mix of skills in-house you’ll need for the present and the future?
- Costs. Is there a healthy balance between labor costs and your organization’s requirements?
- Flexibility. Is your workforce agile and flexible enough to respond to changing market conditions?
Workforce planning makes it easier to optimize your operating costs, gives you greater control over staff turnover, pinpoints potential skill gaps, and helps you develop and implement the right training programs.
Training Within Industry
Training Within Industry (TWI) [5] is a structured approach to training and development that standardizes work processes with a four-pillared framework that encompasses:
- Job instruction
- Job methods
- Job relations
- Program development
These pillars allow new employees to become productive more quickly. TWI also provides you with greater insight into operational and process-related improvements.
Using a skills matrix to improve production processesCopied
A skills matrix can help you track and manage the skills your employees have and need to improve your production processes.
AG5 offers several Excel-based skill matrices that are available to download for free.
- You can read our blog, “5 free skills matrix templates & samples”
- You can download one of our industry-specific skills matrices from our database
- You can create your own using our “Ultimate Guide to Creating an Excel-based Skills Matrix”
Spreadsheet-based skills matrices are a great place to start. However, you may soon find that they are becoming overcomplicated and cumbersome. At that point, it may be time to switch to AG5’s skills management software, which will help you save time and money when improving your production processes by providing you with:
- An easy-to-understand overview of all the skills, certifications, and qualifications your employees possess – and those they need
- The ability to edit and update this information anytime, anywhere
- Create visually appealing skills matrices yourself in less than a minute
- Slice and dice your data any way you need
- Share matrices with any co-workers you want
- Say goodbye to all your version management headaches
- And much more
Want to see how it works? Schedule a free, live, 15-minute demo for a personalized look at how you can use AG5 to optimize and improve production processes in your organization.
Update reason: Refreshed content, added new sections, added sources
Sources Copied
- Change view: Table
-
APA
# | Source title | Description | Publication | Retrieved | Source URL |
---|---|---|---|---|---|
1 | TCO (total cost of ownership) | TechTarget | - | April 12, 2024 | https://www.techtarget.com/sea.. |
2 | TPM (Total Productive Maintenance) | Lean Production | - | April 12, 2024 | https://www.leanproduction.com.. |
3 | The Two Pillars of Lean Management. | Vivek Naik | - | April 12, 2024 | https://vivek-e-naik.medium.co.. |
4 | The Two Pillars of Lean Management | Vivek Naik | - | April 12, 2024 | https://vivek-e-naik.medium.co.. |
5 | What is Performance Support | eLearning Industry | - | April 12, 2024 | https://elearningindustry.com/.. |
6 | What is Training Within Industry (TWI)? | TWI Institute | - | March 12, 2024 | https://www.twi-institute.com/.. |