So, what is TPM?
In this article we explain the concept of Total Productive Maintenance (TPM), its significance in optimizing production processes, and how it can enhance overall equipment effectiveness and organizational performance.
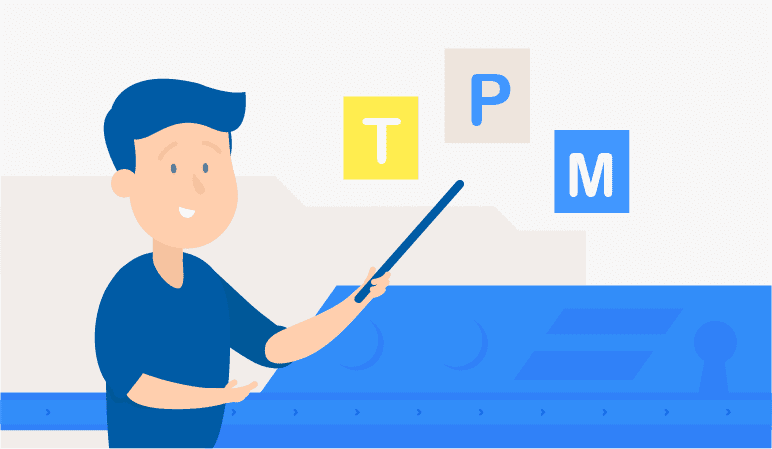
Manufacturers are highly dependent on the quality of their machinery and production lines, especially if they’re manufacturing on an industrial scale. What if an item of machinery or tooling fails or breaks? Or it’s simply not working properly? This can jeopardize or even bring vital operations to a standstill, crippling overall production.
Total Productive Maintenance (TPM) helps you take precautions against the scenarios outlined above. But what is TPM exactly? And why would it be sensible to implement TPM within your organization?
So, what is TPM?Copied
Before we take a closer look at how to implement TPM, it’s worth explaining exactly what Total Productive Maintenance means. TPM is a methodology for servicing and improving manufacturing and quality systems, and the term was coined in 1961 by the Japanese company Nippon Denso – an automotive industry supplier.
Its underlying principle is continuous improvement – continuous improvement of production processes through autonomous and planned maintenance of business-critical machinery.
TPM applies across an entire organization, but focuses in particular on several key areas:
- It attempts to optimize machinery availability through a combination of curative, preventative, and corrective maintenance to achieve the highest possible overall equipment effectiveness (OEE). Achieving this allows machinery to run at maximum output and quality levels.
- TPM embraces the idea that everyone within the company is responsible for machinery maintenance. All employees are actively encouraged to participate and suggest ideas for improvements and all are made aware of the consequences of machinery downtime (‘losses’).
- TPM translates this ‘participation philosophy’ to deploying small, multi-disciplinary teams of well-trained staff, for example operators and maintenance, servicing, and repair technicians. All tasks are standardized to ensure minimal variation.
The 8 TPM pillarsCopied
TPM focuses on maintenance, improvement, and involvement within a framework consisting of eight pillars:
- Focused improvement
- Autonomous maintenance
- Planned maintenance
- Early equipment/product management (EEM/EPM)
- Education & training
- Quality management
- Health, safety & environment (HSE)
- Administrative & office
Let’s take a close look at each of these eight pillars!
1. Focused improvement
The first pillar provides a clear blueprint for your improvement management efforts. You analyze problems by identifying root causes, setting priorities, and listing solutions. Within this pillar, you’re also able to spot trends and respond accordingly.
The main aim of continuous improvement is to eliminate ‘loses’ (short stops, downtime, faults, safety issues, customer complaints, retooling, etc.).
Useful tools or approaches for this first TPM phase include:
- brainstorming
- histograms
- Ishikawa diagrams
- phenomenon & mechanism (PM) analysis
- control charts
- flow diagrams
2. Autonomous maintenance
This pillar establishes a link between ownership and improved technical knowledge levels. But what exactly is the effect of this cross-pollination? It instills a sense that the systems and equipment actually belong to the production workers themselves. This sense of ownership and higher technical understanding, in turn, prompt operators to run their machinery with greater awareness and reduced ‘losses’.
3. Planned maintenance
Planned maintenance focuses primarily on routine servicing by technical services.
The challenge is to minimize unexpected downtime and maintain product quality and productivity levels with only limited resources and without creating unsafe working conditions.
Ways to optimize planned maintenance include:
- training operators properly
- drafting proper maintenance schedules (who, what, when)
- optimizing and standardizing lubricants & lubrication methods
- predicting wear & tear patterns
- implementing and optimizing spare part inventory management
- recording maintenance work in a well-structured information system
- refreshing and maintaining knowledge levels concerning maintenance work
4. Early equipment/product management
Early equipment/product management focuses on optimizing the design of new systems or products.
This phase consists of two separate parts:
- Early equipment management (EEM)
- Early product management (EPM)
The goals are to:
- reduce time to market (TTM)
- guarantee consistently high quality, production rate, and reliability
- minimize total cost of ownership
- create a safe, healthy, and pleasant working environment
5. Education & training
TPM relies wholly on the knowledge and skills of your employees. The aim of this pillar is to transform your company into a learning organization.
Staff should get the opportunity to learn from one another, constantly sharing and retaining knowledge.
TPM uses a system of proficiency levels:
- No knowledge – an employee is not yet able to perform a certain task properly
- Basic knowledge – an employee has the required theoretical knowledge but not the skills required to perform a certain task, job, or role
- Partial experience – an employee is able and permitted to perform certain tasks under supervision
- Independent operator – an employee is able to perform a task without supervision
- Mentor – an employee has sufficient theoretical knowledge and practical experience to perform a task independently, and instruct or supervise others
There are numerous tools and methods available to implement this fifth TPM pillar, for example personal development plans (PDPs), interactive and/or peer-to-peer training, and training courses provided by institutes and suppliers.
6. Quality management
This pillar focuses on establishing a program to improve product quality levels – a balance between stable processes and minimal losses.
It’s important to interpret ‘quality’ in a broad sense – not only machinery and material quality, but also people and working conditions (processes and a safe and pleasant working environment).
Quality matrices are commonly used to help provide greater clarity about quality levels. These depict the preconditions your organization must meet in order to supply high-quality products.
7. Health, safety & environment (HSE)
TPM focuses not only on machinery but also on people.
This seventh pillar addresses the human component in operational processes – health, safety, and the environment.
You can do this in one of several ways.
- The HSE pillar makes everyone responsible for shop-floor safety. It’s up to all levels of an organization to create a safe working environment. Employees are continually informed about the importance of safety, machinery maintenance, and adequate emergency response knowledge and first-aid training.
- Creating awareness is vital. Employees need to be aware of environmental issues that impact the company’s operations and image, for example water usage, emissions, noise levels, waste, and energy consumption.
- They’re also held accountable for maintaining a neat, tidy, well-organized workplace at all times.
It’s also vital that shop floor incidents be reported and discussed openly, making use of behavioral observations and critical task analyses (CTAs).
8. Administration & offices
Although TPM primarily focuses on production and manufacturing, it’s important not to forget administrative departments and offices. After all, it’s from these areas that the production processes are often managed.
This eighth pillar focuses on providing the right information in the right form to the right place at the lowest possible cost. It involves streamlining work processes, removing redundant archives, and training employees.
Why implement TPM?Copied
TPM has many benefits, which is why implementing TPM is certainly worth considering. Here are just a few reasons why it’s worth your while.
1. Less unplanned maintenance
When properly implemented, TPM can reduce unplanned maintenance because it introduces a more structured approach to maintenance and instills a sense of ownership among the operators using your equipment and machinery.
2. Less downtime
Because TPM introduces ongoing and structured quality control procedures, your machinery will be less affected by downtime or faults. Processes will come to a standstill less frequently, and you’ll maintain higher productivity levels.
3. Safer working environment
Because TPM also addresses human issues, it leads to a safer working environment. Employees are expected to keep their workplace neat, tidy, and well-organized, which reduces the likelihood of industrial accidents. What’s more, TPM focuses heavily on cultivating high levels of safety awareness within your workforce.
4. Lower production costs
Faulty or broken machinery and equipment cost money. Because TPM increases the efficiency of your machinery, it also helps you reduce your maintenance and production costs and increase profitability and return on investment (ROI).
5. Measurable results
Another important benefit are tangibly measurable results. TPM goals are measured using overall equipment effectiveness (OEE) – a standard within the manufacturing industry. This metric takes into account your machinery’s availability, performance, and quality and provides a universal framework for benchmarking your manufacturing processes’ efficiency and quality.
Quantify to qualifyCopied
Recording metrics and skills is essential if you want to determine how effective TPM is within your organization. Skills matrices are just one of several tools that can help you in this respect. They have many benefits that can help you implement TPM:
- They greatly simplify workforce planning, especially if employees are off sick or you’re experiencing peaks in demand. Using skills matrices, you know immediately who you can assign to a task and where.
- Skills matrices are also a great means for mapping and tracking team and/or individual progress.
- Both management and staff can use them for general planning purposes, but also for very specific objectives.
- You’ll be able to visualize TPM processes and monitor team and individual growth more easily.
Download a free Excel template to get started with skills management and find out how matrices can help you!
If you’ve already made a start with skills matrices and you’re looking for a tool that provides greater flexibility and versatility, then request a personal demo and get better acquainted with AG5’s skills management software.
Copied
Getting started with TPMCopied
TPM is an effective method for improving your machinery and production process efficiency. It introduces a structured approach to maintenance and quality control. What’s more, TPM creates a prominent role for shop floor personnel by instilling a sense of ownership over the equipment and machinery they use.
Curious how you should implement TPM in your organization? Read our article, ‘7 steps to successful Total Productive Maintenance (TPM)’.