How to achieve smooth, swift, streamlined onboarding? Training within industry. That’s how!
Read about the essence of Training Within Industry (TWI) in this article, exploring its core principles and real-world applications to optimize workforce training and operational effectiveness.
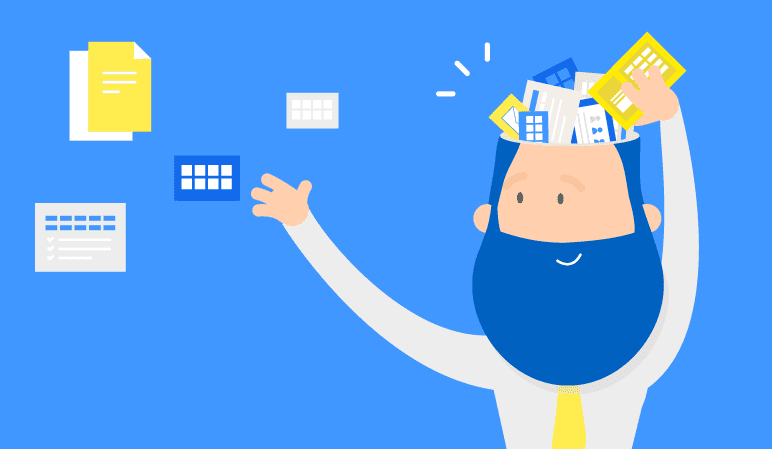
Many companies invest time, money, and resources in staff training to improve quality levels, corporate culture, or cost management. The return on investment is often slow to materialize and in practice difficult to quantify.
Training Within Industry (TWI) is a method for training staff quickly and effectively. According to some trainers, it’s the most effective method available.
But what is TWI exactly? What are its underlying principles? And why has it been growing in popularity so much in the past two years? We’ll be providing answers to all these questions in this article.
What is TWI?Copied
Training Within Industry has its origins in the United States. The United States Department of War – the forerunner to the Ministry of Defense – developed the concept between 1940 and 1945.
Its purpose was to be able to continue providing services as part of the war effort in response to reduced staffing levels. American industry lost a lot of its personnel to the armed forces when the US entered the Second World War. This resulted in a shortage of skilled labor, which meant that new staff had to be trained quickly and effectively.
After the war, the TWI method spread around the world. Japanese companies, such as Toyota, eagerly and enthusiastically embraced the concept during reconstruction, as well as many others within the business world.
TWI is broadly viewed as the foundations of flexible training programs such as Kaizen and Lean. It consists of four modules. In its original form, each of the training sessions lasted ten hours.
TWI modulesCopied
To understand TWI more fully, it’s important to examine its components more closely.
1. Job Instruction (JI)
The first TWI module is ‘Job Instruction’. Team leaders are trained how to get unexperienced operators working according to standard operating procedures (SOPs) so that they can perform repetitive tasks more effectively and efficiently.
The module was developed based on scientific observations – as are most of the other TWI modules. In the JI module, participants learn how to analyze and dissect tasks and then how to instruct others most effectively. Effective instruction involves personnel learning, internalizing, and remembering how to perform tasks quickly and efficiently according to agreed best practices.
JI divides tasks and operational processes into small, well defined steps with key focus areas (or ‘key points’), which the instructor clearly explains and substantiates.
We usually split JI into four phases:
- Prepare – the instructor prepares the operator for the skill to be learned, for example, by relating it to a skill the operator has already mastered.
- Present – the instructor demonstrates each step and highlights the hows and whys underlying the key points.
- Try out – the operator gradually puts the theory into practice. The instructor allows the operator to perform the task independently, reiterating the hows and whys underlying the key points (learning by doing).
- Follow up – the instructor checks whether the operator can perform all the tasks independently and assigns someone to whom the operator can turn for help or advice if needed.
2. Job Methods (JM)
Job Instruction trains team leaders how to instruct future operators about the importance of SOPs. The second TWI module – Job Methods – takes this a step further and focuses on improving the SOPs introduced during JI.
The main purpose of JM is to improve procedures continually and incrementally. We also split JM into four steps as we did for JI:
- Break down – this phase examines each of the SOP steps in more detail.
- Question – this phase makes personnel question each step of the tried-and-trusted SOP. What is its purpose? Why is each step necessary?
- Develop – this phase takes any information gleaned from breakdown and questioning to improve and hone the SOPs, for example, eliminating unnecessary steps, reordering activities, or combining tasks.
- Apply – this phase involves the operator presenting revised SOPs to managers and fellow operators, paying close attention to safety, quality, quantity, and costs. If everyone’s happy, then the new SOP is introduced as the new standard!
3. Job Relations (JR)
The JR module focuses on improving working relations and trains team leaders how to deal with co workers effectively and how to maximize their strengths and qualities.
The key JR motto is, “People should be treated as individuals.”
Properly implementing JR entails creating plenty of room for soft skills.
4. Program Development (PD)
The PD module plays a role at a higher level than the previous three TWI modules. It effectively forms the first concrete step towards selecting and implementing large-scale organizational improvement projects in a structured fashion.
TWI benefitsCopied
In the past few years, we’ve seen an increasing number of organizations getting to grips with TWI. Many are striving for lean or agile operations to work faster and more efficiently. The recent economic crisis and increasing competition across many sectors have also been forcing companies to streamline their production processes using only modest means. Training Within Industry was just the right approach.
Recent developments have pushed TWI’s benefits into the spotlight as a method that helps companies onboard new staff and temporary workers quickly and cost-effectively.
Here are the key benefits:
- SOPs help create a sense of stability and certainty, boosting productivity and quality. Some case studies demonstrated that it’s possible to achieve 90% fewer errors and 26% higher productivity within only six months.
- Personnel can be assigned to producing high-quality products faster when working to SOPs.
- Machinery and production line startup times can be reduced by up to 75%.
- Experienced personnel can share their knowledge and experience and instruct younger or less experienced co-workers in an inspiring way.
- TWI offers ways to improve working relations and increase engagement levels.
- It creates greater transparency and understanding for operational and process-based improvement projects.
TWI in practiceCopied
TWI is gaining traction around the world – partly in response to the TWI Institute’s platform. But also in the Netherlands, TWI is being put into practice with organizations such as the TWI Company (Dutch) leading the way.
The TWI Company has, however, taken the method to an even higher level and has justifiably tagged its approach as TWI 2.0 (Dutch). For example, the organization offers custom-made TWI training, certification, and accreditation programs and helps companies implement TWI methods.
What’s more, they have plenty of case studies that demonstrate the added value that TWI provides in daily business situations.
LEGO & TWI
You’d have to be living under a rock to be unaware of LEGO and the company’s colorful building blocks! What few among us know, however, is that LEGO is one of TWI’s most successful case studies. A book has even been written about it.
This book examines how LEGO successfully and rapidly achieved unrivaled knowledge transfer throughout its organization despite language and cultural barriers.
The results were particularly impressive:
- time reductions from 200 to 60 minutes on the general production line
- onboarding in some parts of the company reduced from twelve to three months
- improved staff-management expectations and greater stability
TWI 2.0 at Johma
Johma is a food company that uses TWI to improve and streamline its operating procedures. This is vital to the company because it works with a lot of temping staff who have to be onboarded quickly and effectively.
Johma started rolling out TWI within its organization in 2012 – with the assistance of the TWI Company. In this time, a third of the company has implemented TWI.
Its implementation has allowed Johma to make big steps towards improving repetitive working processes:
- It helps determine quickly whether someone has picked up a particular operating procedure. Johma then knows much earlier whether it’s taken on competent personnel. Two weeks after completion of the onboarding course, an audit is conducted of both the trainers and participants to determine whether they have mastered the skills sufficiently.
- TWI helped cut onboarding times significantly. In the cold kitchen department, where salads are prepared, onboarding used to take six months, but now only takes six to eight weeks. This has also cut costs significantly – sometimes between hundreds and thousands of euros per employee.
- TWI-based production lines are stable and experience virtually zero downtime.
TWI 2.0 at Stiho
Stiho is a building materials wholesaler that also introduced TWI with the help of the TWI Company. The OLÉ Project (Organization/Logistics/Effectiveness) optimized its logistics processes at its location in Utrecht, making them safer, better, and faster.
Stiho makes extensive use of TWI – like Starbucks, LEGO, and McDonald’s before it – to train and onboard its personnel quickly, safely, and consistently. The result is that everyone works in the same way, guaranteeing higher quality levels.
Stiho also uses the following tools as part of its TWI methods:
- departmental baseline measurements to identify bottlenecks and potential solutions
- departmental key performance indicators to determine whether daily operations are running smoothly and to identify issues for upcoming days
TWI & AG5Copied
If you’d like to implement Training Within Industry in your organization, it’s worth taking the time to consider the administrative aspects of doing so:
- Who has which skills and has mastered which SOPs?
- Which departments have completed which phases of TWI training?
- What still needs to be addressed within which departments to safeguard SOPs?
AG5’s skills management software provides a solution that keeps track of all these issues. What’s more, all the information is stored in a single centralized location, streamlining TWI adoption significantly.
Conclusion – TWI is the future!Copied
TWI’s main strength is that it harnesses the power of standardization to constantly improve processes. It allows you to make significant progress in terms of efficiency and speed at minimal cost.
If you’d like to find out more about TWI, or you’re looking for software to help you with your TWI implementation, please get in touch with us at AG5 or one of the TWI Company’s specialists.