10 Wege zur Verbesserung und Optimierung Ihrer Produktionsprozesse
In der Fertigungsbranche sind effiziente Produktionsprozesse der Motor für Ihren Unternehmenserfolg. Sie helfen Unternehmen, effizienter, effektiver und sicherer zu arbeiten. Für die Optimierung Ihrer Produktionsprozesse ist ein umfassender Ansatz erforderlich, der Ihre Mitarbeiter:innen, Maschinen und Werkzeuge gleichermaßen berücksichtigt. Darüber hinaus benötigen Sie fortschrittliche Technologien, um die Kompetenzen, Zertifizierungen und Qualifikationen Ihrer Produktionsmittel effektiv zu verfolgen und zu verwalten. In diesem...
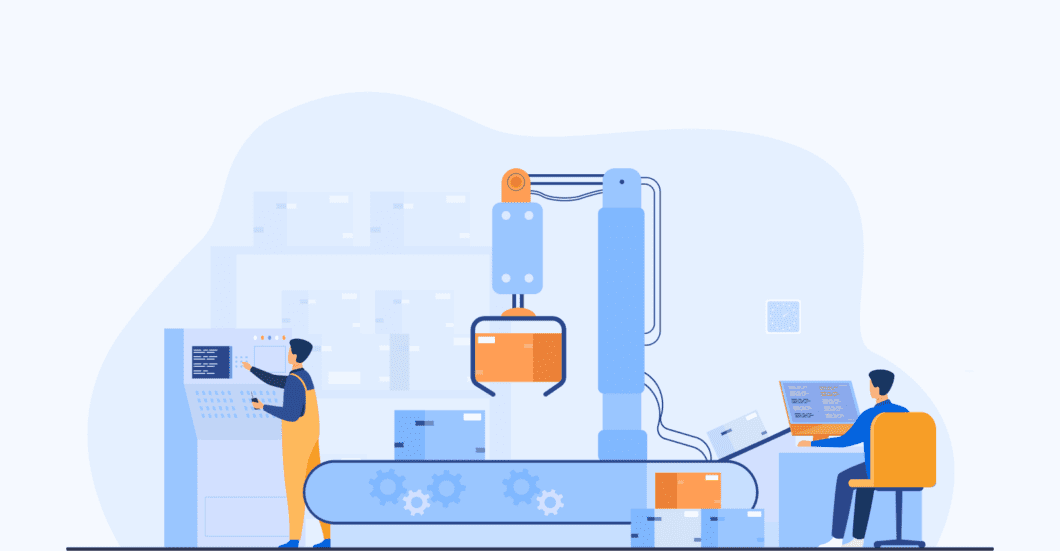
In der Fertigungsbranche sind effiziente Produktionsprozesse der Motor für Ihren Unternehmenserfolg. Sie helfen Unternehmen, effizienter, effektiver und sicherer zu arbeiten.
Für die Optimierung Ihrer Produktionsprozesse ist ein umfassender Ansatz erforderlich, der Ihre Mitarbeiter:innen, Maschinen und Werkzeuge gleichermaßen berücksichtigt. Darüber hinaus benötigen Sie fortschrittliche Technologien, um die Kompetenzen, Zertifizierungen und Qualifikationen Ihrer Produktionsmittel effektiv zu verfolgen und zu verwalten.
In diesem Artikel geben wir Ihnen Tipps, Tricks und Strategien für die Entwicklung und Umsetzung dieses Ansatzes. Außerdem zeigen wir Ihnen, wie Sie Ihre Produktionsprozesse mit der Skills Management Software von AG5 verbessern können.
Vorteile der Verbesserung der ProduktionsprozesseCopied
Bevor wir ins Detail gehen, betrachten wir die Bedeutung der Optimierung Ihrer Produktionsprozesse aus der Sicht der Vorteile, die sich daraus für Ihr Unternehmen ergeben.
- Produktivitätssteigerung. Durch regelmäßige und detaillierte Prozessanalysen können Sie Ineffizienzen und Engpässe schnell erkennen und beheben, zukünftige Herausforderungen antizipieren und Ihre Arbeitsabläufe kontinuierlich optimieren.
- Schnellere Markteinführung. Durch effizientes Arbeiten können Sie ein qualitativ hochwertiges Produkt schneller auf den Markt bringen.
- Verbesserung der Produktqualität. Ausführliche Tests wirken sich auch positiv auf andere wichtige Produkteigenschaften wie Leistung, Lebensdauer, Benutzerfreundlichkeit und Sicherheit aus.
- Höhere Kundenzufriedenheit und Kundenbindung. Die Herstellung eines qualitativ hochwertigen Produkts fördert die Kundenbindung und stärkt Ihre Wettbewerbsposition durch die Schaffung einer treuen Stammkundschaft.
Herausforderungen bei der Optimierung von ProduktionsprozessenCopied
Lassen Sie uns auch einen kurzen Blick auf einige der Herausforderungen werfen, mit denen unsere Kunden in der Fertigungsindustrie bei der Verbesserung ihrer Produktionsprozesse häufig konfrontiert sind, sowie auf Lösungsansätze, um diese zu vermeiden.
Mangel an klaren Zielen. Uneindeutigkeit kann zu Meinungsverschiedenheiten unter den Mitarbeiter:innen und zur Verschwendung von Ressourcen führen. Setzen Sie deshalb klare und spezifische Ziele für jede Verbesserung, um sicherzustellen, dass alle auf dasselbe Ziel hinarbeiten.
Vernachlässigung des Veränderungsmanagements. Die Optimierung von Produktionsprozessen erfordert oft Veränderungen von Arbeitsabläufen, Verantwortlichkeiten und der Unternehmenskultur. Daher ist es wichtig, Maßnahmen zu ergreifen, um sicherzustellen, dass Ihre Mitarbeiter:innen die eingeführten Veränderungen verstehen und unterstützen. So können Widerstände und Rückschläge vermieden werden.
Konzentration auf kurzfristige Ziele. Schnelle Erfolge sind wichtig, aber wenn Sie sich nur auf kurzfristige Gewinne konzentrieren, können Sie die langfristige Nachhaltigkeit und Skalierbarkeit Ihrer neuen Produktionsprozesse vernachlässigen.
6 Tipps zur Verbesserung des ProduktionsprozessesCopied
Nutzen Sie die folgenden Tipps, um Ihre Produktionsprozesse sofort zu optimieren.
1. Analysieren Sie Ihre aktuellen Arbeitsabläufe
Um von A nach B zu kommen, muss man zunächst wissen, wo A ist. Betrachten Sie deshalb Ihre Arbeitsabläufe aus drei verschiedenen Perspektiven Betrachten Sie daher Ihre Arbeitsabläufe aus drei verschiedenen Perspektiven
- Personal. Sind die richtigen Personen mit den richtigen Fähigkeiten zur richtigen Zeit am richtigen Ort? Haben Sie klare, SMART formulierte Ziele (erreichbar und überprüfbar zu sein, spezifisch, messbar, attraktiv, realistisch und terminiert) für Ihre Produktionsprozesse definiert?
- Prozesse. Sie zuletzt Ihre Prozesse erfasst und bewertet? Wo gibt es Engpässe und Hindernisse? Wo könnten Engpässe und Hindernisse auftreten?
- Werkzeuge und Technologie. Sind Ihre Maschinen und Anlagen in gutem Zustand? Setzen Sie die effizienteste Technologie ein? Und wie flexibel sind Sie bei der Anpassung Ihrer Produktionsprozesse?
2. Modernisieren Sie Ihre Prozesse und Technologien
Sobald Sie Ihre aktuellen Arbeitsabläufe erfasst und bewertet haben, können Sie entscheiden, ob eine Modernisierung oder Verbesserung Ihrer Prozesse und Technologien erforderlich ist.
- Können bestimmte Prozesse automatisiert werden?
- Setzen Sie Software ein, um Ihre Planung, Bestandskontrolle oder Überwachung zu optimieren?
- Ersetzen oder modernisieren Sie Ihre Maschinen und Anlagen?
Tipp: Vergessen Sie nicht, die Gesamtkosten (Total Cost of Ownership, TCO) [1]für jede neue Technologie oder Ausrüstung, die Sie einführen möchten, zu berücksichtigen. Diese umfassen die Kosten für den Kauf, die Implementierung, die Nutzung und sogar die Außerbetriebnahme von Geräten, Maschinen, Werkzeugen, Software oder anderen Anlagen in Ihrem Unternehmen.
3. Behalten Sie geplante Wartungsarbeiten im Blick
Eine der Hauptursachen für ineffiziente Produktionsprozesse ist häufig das Fehlen geplanter Instandhaltung. Defekte oder verschlissene Maschinen verursachen weitaus höhere Kosten als regelmäßige Wartungseinsätze.
Beachten Sie folgende Punkte:
- Schulen Sie Ihre Bediener und Wartungstechniker, damit sie bei Problemen mit Anlagen oder Maschinen schnell und effektiv reagieren können.
- Legen Sie regelmäßig feste Termine und Zeiten für die geplante Wartung fest.
- Ermitteln Sie gemeinsam mit Ihrem Produktionspersonal die optimalen Zeitfenster für geplante Wartungsarbeiten.
Tipp: Lesen Sie unseren Artikel „Was ist TPM (Total Productive Maintenance)?“, um mehr über Total Productive Maintenance zu erfahren – eine Methode der geplanten Instandhaltung, die Ihrem Unternehmen helfen kann, kostspielige Ausfallzeiten aufgrund reparaturbedürftiger Geräte oder Maschinen zu vermeiden. [2]
4. Erarbeiten Sie maßgeschneiderte Schulungspläne für Ihre Mitarbeiter:innen
Je besser Ihre Mitarbeiter:innen in der Bedienung und Wartung Ihrer Maschinen und Anlagen geschult sind, desto geringer ist das Risiko kostspieliger Ausfallzeiten.
Ihren Mitarbeiter:innen sollte die Möglichkeit geboten werden, neue Fähigkeiten zu erwerben, an Schulungen teilzunehmen und erforderliche Zertifizierungen zu erlangen. Um dies zu ermöglichen, ist es wichtig, die Fähigkeiten, Qualifikationen und Zertifizierungen Ihrer Mitarbeiter:innen zu verfolgen und zu verwalten – sowohl die bereits vorhandenen als auch die benötigten.
5. Sauberkeit und Ordnung am Arbeitsplatz aufrechterhalten
Ein gut organisierter Arbeitsplatz ist entscheidend für optimierte Produktionsprozesse und ist vielleicht der wichtigste Aspekt der allgemeinen Arbeitssicherheit.
Optimieren Sie die Arbeitsplatzgestaltung: Ordnen, sortieren und beschriften Sie Handwerkzeuge, damit sie leicht zu finden sind. Versuchen Sie, die Wege zwischen Werkzeugen und Maschinen so kurz wie möglich zu halten. Das macht den Arbeitsplatz effizienter und sicherer!
6. Achten Sie auf eine ausgewogene Lagerhaltung
Vergewissern Sie sich, dass Sie genau wissen, was sich im Lager befindet und wo es sich befindet. Vermeiden Sie Überbestände und minimieren Sie das Risiko von Fehlbeständen.
Verwenden Sie Software zur Bestandsverwaltung, um den Materialbedarf zu prognostizieren und automatische Benachrichtigungen zu erhalten. So können Sie sicherstellen, dass Sie das richtige Gleichgewicht zwischen Über- und Unterbeständen halten.
4 Beispiele für Strategien zur Optimierung Ihrer ProduktionsprozesseCopied
Die verbleibenden sechs Möglichkeiten zur Verbesserung Ihrer Produktionsprozesse konzentrieren sich auf Maßnahmen, die Sie in Ihrem Unternehmen umsetzen können, um einen reibungslosen Ablauf Ihrer Prozesse zu gewährleisten.
Kontinuierliche Verbesserung
Kontinuierliche Verbesserung ist einer der Grundpfeiler des Lean-Ansatzes. [3] Unternehmen setzen dabei Schritte, um Produktivität, Qualität, Kosten und Durchlaufzeit schrittweise und iterativ zu optimieren, anstatt eine einmalige, groß angelegte Veränderung vorzunehmen.
Kontinuierliche Verbesserung bedeutet, dass die Optimierung von Produktionsprozessen ein fortlaufender Prozess ist, der maßgeblich von den Mitarbeiter:innen beeinflusst wird, die Veränderungen und Verbesserungen umsetzen. Aus diesem Grund ist es wichtig, Schulungen und Coaching am Arbeitsplatz anzubieten, um die Mitarbeiter:innen in die Lage zu versetzen, sich in den Produktionsprozessen kontinuierlich weiterzuentwickeln.
Kontinuierliche Verbesserung besteht aus drei Hauptphasen:
- Vorschläge sammeln. Das Problem mit Hilfe der gesammelten Vorschläge, Rückmeldungen oder Ideen lösen.
- Feedback umsetzen. Lösen Sie das Problem mit Hilfe der gesammelten Vorschläge, Rückmeldungen oder Ideen.
- Überwachen und lernen. Bewertung der Wirksamkeit der umgesetzten Lösungen.
Leistungsunterstützung
Leistungsunterstützung bzw. Performance Support ist eine Methode zur Optimierung von Produktionsprozessen, die auf praktischem Lernen beruht. [4] Sie beinhaltet die Schaffung von „Lernmomenten“, die speziell auf die praktischen Bedürfnisse der Mitarbeiter:innen zugeschnitten sind.
Diese Leistungsunterstützung besteht aus fünf „Bedarfsmomenten“.
- Neu. Die Notwendigkeit, etwas Neues zu lernen oder neue Fähigkeiten zu erwerben.
- Vertiefen.Die Notwendigkeit, mehr über ein bestimmtes Thema oder eine bestimmte Arbeitsmethode zu erfahren.
- Praxis. Die Notwendigkeit, Informationen, Fähigkeiten oder Verfahren in die Praxis umzusetzen.
- Veränderung. Die Notwendigkeit, mit Veränderungen Schritt zu halten und sich anzupassen.
- Problemlösung.Die Notwendigkeit, Probleme anzugehen und zu lösen.
Personalplanung.
Ziel der Personalplanung ist es, die Prioritäten und Anforderungen eines Unternehmens mit dem vorhandenen Personal in Einklang zu bringen. Dabei geht es vor allem um Faktoren wie:
- Umfang. Haben Sie derzeit viele offene Stellen zu besetzen?
- Mischung. Verfügen Sie intern über die richtige Mischung von Fähigkeiten, die Sie jetzt und in Zukunft benötigen?
- Kosten. Stehen die Arbeitskosten in einem ausgewogenen Verhältnis zu den Anforderungen Ihres Unternehmens?
- Flexibilität. Ist Ihre Belegschaft agil und flexibel genug, um auf sich verändernde Marktbedingungen zu reagieren?
Die Personalplanung unterstützt Sie bei der Optimierung Ihrer Betriebskosten, der Kontrolle der Personalfluktuation, der Ermittlung potenzieller Kompetenzlücken und der Entwicklung und Umsetzung gezielter Weiterbildungsprogramme.
Ausbildung am Arbeitsplatz
Ausbildung am Arbeitsplatz (Training Within Industry, TWI) [5] ist ein strukturierter Ansatz für Ausbildung und Entwicklung in der Industrie. Dieser Ansatz standardisiert die Arbeitsprozesse mit Hilfe eines Vier-Säulen-Rahmens, der folgende Elemente umfasst
- Arbeitsanweisungen
- Arbeitsmethoden
- Arbeitsbeziehungen
- Entwicklungsprogramme
Diese Säulen dienen dazu, neuen Mitarbeiter:innen einen schnelleren Einstieg in die Produktivität zu ermöglichen. Die Ausbildung am Arbeitsplatz bietet auch Einblicke in betriebliche und prozessbezogene Verbesserungen.
Steigern Sie die Effizienz Ihrer Produktionsprozesse mit einer Qualifikationsmatrix.Copied
Diese ermöglicht es Ihnen, die Fähigkeiten Ihrer Mitarbeiter:innen zu verfolgen und zu verwalten, um kontinuierliche Verbesserungen zu erzielen.
AG5 bietet mehrere Excel-basierte Qualifikationsmatrizen zum kostenlosen Download an.
- Lesen Sie unseren Blog „5 kostenlose Qualifikationsmatrix-Vorlagen und Beispiele“.
- Sie können eine unserer branchenspezifischen Qualifikationsmatrizen aus unserer Datenbank herunterladen.
- Sie können Ihre eigene erstellen, indem Sie unseren „ultimativen Leitfaden zum Erstellen einer Excel-basierten Qualifikationsmatrix“ verwenden.
Tabellenbasierte Qualifikationsmatrizen sind zwar ein guter Ausgangspunkt, können aber schnell zu kompliziert und umständlich werden. In diesem Fall ist es vielleicht an der Zeit, auf die Skills Management Software von AG5 umzusteigen. Sie kann Ihnen helfen, Zeit und Geld bei der Optimierung Ihrer Produktionsprozesse zu sparen. Und zwar durch:
- Übersichtlicher Einblick in die vorhandenen und benötigten Fähigkeiten, Zertifizierungen und Qualifikationen Ihrer Mitarbeiter:innen.
- Sie können diese Informationen jederzeit und überall bearbeiten und aktualisieren.
- Erstellen von visuell ansprechenden Qualifikationsmatrizen in weniger als einer Minute.
- Die Daten so aufbereiten, wie es für Ihr Unternehmen am nützlichsten ist.
- Nutzen der Matrizen mit beliebigen Arbeitskolleg:innen.
- Verabschieden Sie sich von allen Problemen der Versionsverwaltung
- Und vieles mehr.
Wollen Sie sehen, wie es funktioniert? Vereinbaren Sie noch heute einen Termin für eine kostenlose 15-minütige Live-Demo und erfahren Sie, wie Sie mit AG5 die Produktionsprozesse in Ihrem Unternehmen optimieren und verbessern können.
Grund für die Aktualisierung: Inhalt aktualisiert, neue Abschnitte hinzugefügt, Quellen hinzugefügt.
Quellen Copied
- Change view: Table
-
APA
# | Source title | Description | Publication | Retrieved | Source URL |
---|---|---|---|---|---|
1 | TCO (total cost of ownership) | TechTarget | - | April 12, 2024 | https://www.techtarget.com/sea.. |
2 | TPM (Total Productive Maintenance) | Lean Production | - | April 12, 2024 | https://www.leanproduction.com.. |
3 | The Two Pillars of Lean Management. | Vivek Naik | - | April 12, 2024 | https://vivek-e-naik.medium.co.. |
4 | The Two Pillars of Lean Management | Vivek Naik | - | April 12, 2024 | https://vivek-e-naik.medium.co.. |
5 | What is Performance Support | eLearning Industry | - | April 12, 2024 | https://elearningindustry.com/.. |
6 | What is Training Within Industry (TWI)? | TWI Institute | - | March 12, 2024 | https://www.twi-institute.com/.. |