11 benefits of continuous improvement to future‑ready organizations
During this article we explore the 11 benefits of continuous improvement for future-ready organizations. Discover how to thrive in a rapidly evolving landscape.
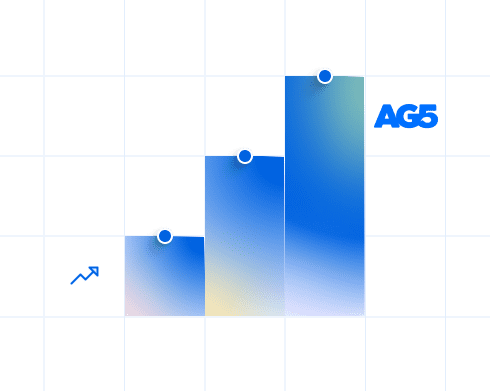
Customer demands and market requirements are changing faster than ever. It’s no longer enough to merely ‘dust off’ your processes every now and then. Continuous improvement is the best way to become and to remain future-ready!
What is continuous improvement?Copied
Continuous improvement (CI) is the ongoing effort to enhance processes, products, or services by making incremental changes over time. It focuses on identifying inefficiencies, reducing waste, and optimizing performance through regular assessment and refinement – and is critical in achieving and maintaining a competitive edge [1].
Here are a few of the key aspects of continuous improvement:
- Small, incremental changes rather than drastic overhauls
- Employee involvement, encouraging feedback and participation
- Data-driven decision-making, using metrics to guide improvements
- Sustained long-term effort, rather than one-time initiatives
Process improvement types
There are several established methodologies that organizations commonly use in their CI efforts. Despite their differences, these methodologies all focus on improving efficiency, reducing waste, and improving the quality of products or services.
- LEAN principles. This methodology helps ensure that materials and labor are used effectively, minimizing delays and excess inventory. It is ideal for optimizing workflows, reducing waste, and improving efficiency in production lines.
- Six Sigma. A data-driven approach that focuses on reducing defects and variability in manufacturing processes through statistical analysis, leading to higher product quality and consistency [2].
- Total Quality Management (TQM). Emphasizes continuous improvement in all aspects of an organization by fostering a quality-focused culture and involving employees at all levels. An example here would be an organization training all employees in quality control techniques, ensuring every stage of production meets strict quality standards [3].
- Kaizen. A philosophy of continuous improvement originating in Japan, Kaizen encourages incremental changes involving all employees. A manufacturing team, for example, could hold daily stand-up meetings to identify small workflow improvements that can enhance overall productivity.
The continuous improvement methodology you choose depends on your organization, existing processes, and specific goals or needs. In our experience, however, the most popular for manufacturing or manufacturing-adjacent organizations are LEAN principles and Six Sigma, as they both offer structured, data-driven approaches that specifically target waste elimination, process optimization, and defect reduction. This means they are particularly effective in high-production environments.
3 steps towards continuous improvementCopied
Once you’ve decided on a CI methodology, you’ll need to create a plan for its implementation. You should focus on three factors: when, where, and key considerations. Here, we’ll explore each.
1. Where to implement continuous improvement processes
- Production floors. This is where most of the operational work happens, and where inefficiencies can lead to higher costs or reduced quality. Implementing CI on production floors – or within specific processes – allows for immediate, localized improvements that can significantly impact productivity
- Departments or teams. Implementing CI within specific departments (for example, manufacturing, quality control, or logistics) allows for targeted improvements based on the unique challenges and goals of that department
- Across the organization. In larger organizations – especially those spread across multiple sites – CI should be implemented at the organizational level alignment. This drives a culture of continuous improvement where all employees are motivated to contribute, whether in safety initiatives, sustainability programs, or digital transformation-focused projects
2. When to implement continuous improvement processes
Next, think about when you should implement a continuous improvement process. A few common times to do this are:
- During regular review cycles
- When problems or inefficiencies are identified
- During transitions or upgrades – such as when new technologies, systems, or processes are introduced
- As part of a cultural shift or organizational change
- In response to customer or client feedback
3. Key considerations for implementing continuous improvement processes
Finally, you should think about several additional CI-related factors that will affect how smoothly your processes run.
- Timing. CI should be an ongoing effort rather than a one-time intervention.
- Flexibility. Regular reviews are important, but flexibility is also key. If urgent problems arise, CI processes should be implemented quickly to address them.
- Employee involvement. The timing of CI is also linked to when employees are most receptive to changes. Ensure that training, support, and communication align with improvement initiatives to maximize engagement.
What are the benefits of continuous improvement?Copied
Why adopt continuous improvement? What are the benefits of working in this way? Let’s take a closer look at some of the foremost benefits of continuous improvement.
1. Greater employee engagement
Employees who experience higher job satisfaction levels and are more engaged with your company can be powerful agents for change and improvement. For example, research conducted by Towers Perrin revealed that companies with high employee engagement levels have 19.2% higher operating incomes than their competitors with lower levels.
Continuous improvement gives staff the basis they need to solve the problems they encounter in their work themselves. This not only improves efficiency, but also sends the signal to your staff that you appreciate and value them and their vision.
2. Reduced staff turnover
Satisfied, engaged employees are often more loyal. That’s why continuous improvement is a great way to help reduce staff turnover. Which is great news because high staff turnover is detrimental to your company’s operational continuity. Reducing it helps cut the amount of time and money you need to invest in recruitment, selection, onboarding, and retraining.
3. Improved customer service
Continuous improvement creates a framework that gives you better insights into your customers’ needs and requirements. What are your customers looking for? What problems are they encountering? And which products or services create the most value for your customers? Armed with the answers to these questions, you can anticipate customers’ needs and requirements more quickly and accurately.
4. A more proactive learning culture
Knowledge rapidly becomes outdated in this fast-paced digital era. But continuous improvement forces you to constantly investigate what could be different, better, more efficient … In short, it creates a proactive learning culture that encourages staff to follow the path least trodden, to learn new things, and to think outside of the box.
5. Higher-quality products & services
Because continuous improvement focuses on making small, incremental improvements to your processes, it also boosts your products and services’ market value. By making your processes more efficient and reducing waste, you’ll also increase your profit margins!
6. Higher productivity
Eliminating superfluous steps makes your processes more efficient as a whole and reduces throughput times. In other words, you can do more in less time and your productivity increases.
7. Faster delivery
If you’re producing more products faster, then your time to market is shorter. This gives you a competitive edge over your competitors who take longer to get their products to market.
8. Lower error ratio
Your error rate will also start to decline as you continue to improve your processes. Quality levels will increase significantly, which is good for your reputation and positioning.
9. Safer workplace
Continuous improvement also involves paying attention to the quality of the workplace. Is everything neat and tidy? Are processes, machinery, and workspaces safe to use? Continuous improvement should also provide answers to this type of question and make safety in the workplace a top priority.
10. Better insight into objectives & strategies
Continuous improvement also raises knowledge levels among employees about your organization’s objectives. Terms such as ‘strategy’ and ‘core values’ then take on greater meaning for your entire workforce.
11. Greater focus on innovation
In the current economic climate, change is the only constant. Today’s innovations may be totally outdated in six months’ time. Continuous improvement encourages agility and increases adaptability. Vital for any company looking to remain relevant in the future!
Continuous improvement & skills managementCopied
You can get the most out of your processes and operations by combining continuous improvement with skills management. Because skills management helps visualize your staff’s skills and competences, it becomes much easier for you to find the right people for the right task.
This combination also makes it easier to monitor your staff’s progress and to respond adequately and effectively to employees off sick or peak periods.
Read our article, How continuous improvement and skills management go hand in hand to find out more.
It’s also important to use the right tools for the job. Download these templates to find out how skills matrices can help you reap the rewards of continuous improvement and skills management combined.
But chances are that after a while you’ll want to take your skills management system to the next level. In which case, schedule a free demo to discover the benefits of AG5’s skills management software!
Use AG5 to identify skill gaps
Say goodbye to Excel matrices. Start using AG5’s plug and play skill matrix software.
ISO27001 certified
Start your 14-day free trial
Sources Copied
- Change view: Table
-
APA
# | Source title | Description | Publication | Retrieved | Source URL |
---|---|---|---|---|---|
1 | How continuous improvement can build a competitive edge | McKinsey | May 6, 2019 | March 5, 2025 | https://www.mckinsey.com/capab.. |
2 | What is Six Sigma? | American Society for Quality | December 1, 2024 | March 5, 2025 | https://asq.org/quality-resour.. |
3 | Total Quality Management | American Society for Quality | November 1, 2024 | March 5, 2025 | https://asq.org/quality-resour.. |