Total Productive Maintenance (TPM) successful implementation: 7 steps
During this article, we explain the seven essential steps for implementing Total Productive Maintenance (TPM) and how it can revolutionize your organization’s approach to maintenance and operational efficiency.
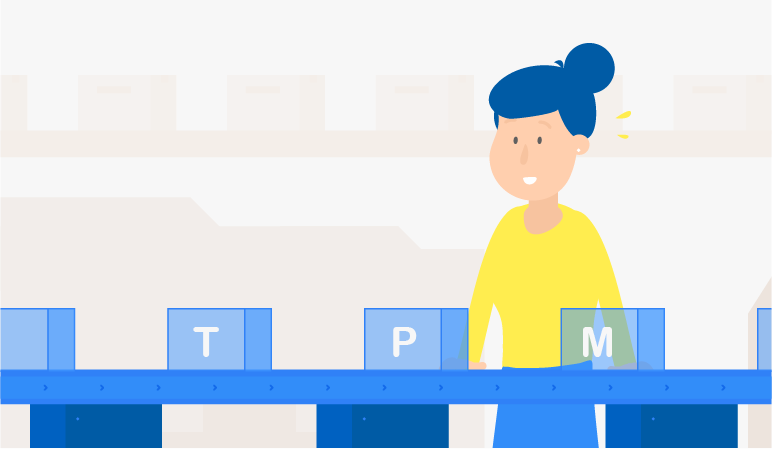
Total Productive Maintenance (TPM) helps keep your machinery and equipment in reliable working order. But does a TPM implementation plan look like in practice? And which steps should you take to integrate this methodology into your existing operational and maintenance procedures?
Read on. We’ll show what, how, and why!
So, what is TPM?Copied
TPM originated in the Japanese industrial sector. Its aim is to help maintain and improve production systems. TPM tackles this across a full spectrum, involving all employees at all levels in the maintenance and servicing of their organization’s equipment and machinery.
Applying the principles properly will help you minimize the likelihood of equipment failures and maximize productivity and continuity. What’s more, TPM helps raise awareness among employees about technology, safety, and the environment because it instils a sense of ownership of the equipment and machinery they work with on a daily basis.
TPM comprises eight pillars:
- Focused improvement
- Autonomous maintenance
- Planned maintenance
- Early equipment/product management
- Education & training
- Quality management
- Health, safety & environment (HSE)
- Administration & office
Find out more in our article, ‘So, what is TPM?’.
Step by step to successful TPMCopied
But how should you implement TPM in practice? We’ll explain how in the following steps.
Step 1: Share your plans with your entire organization
TPM only works if everyone within your organization understands its main objectives and the value it brings to the table. But above all it’s critical that management and supervisors grasp the importance of proper TPM procedures. If managers promote, introduce, and adopt a certain way of working, then shop-floor personnel will generally embrace plans much faster.
Step 2: Identify suitable systems, machinery, or processes
Step 2 involves identifying a suitable part of your working environment where you can conduct a TPM pilot test. This could be a specific item of machinery or a system, or even part of a production process that isn’t running particularly smoothly.
Pinpoint which elements would give you a quick win. The SMART method is a useful means for making this selection. SMART stands for specific, measurable, achievable, realistic, and time-related.
Step 3: Get equipment into optimal working condition
Step 3 involves getting started with your pilot test. Define the parameters that the equipment or processes you identified in Step 2 should satisfy. The 5S system is a useful tool for doing this because it forces you to define the improvements you’re seeking – sort, set, shine, standardize, sustain.
Start by taking photos of the ‘old situation’.
Next, tackle the workspace, removing clutter and any spare parts and tools left lying around. Then, clean all the machinery and equipment and take a photo of the workspace in the ‘new situation’. Audits allow you to determine whether staff are keeping workspaces neat and tidy over the longer term.
Now you have a clearer picture of the equipment and machinery and its current state, you can start drafting an autonomous maintenance plan. This plan details how to maintain your machinery and workplace, and clearly defines who does what and when.
Step 4: Measure overall equipment effectiveness
Step 4 involves measuring and gathering data so that you can start creating an optimally arranged and efficient production environment. The best way to do this is to use the concept of overall equipment effectiveness (OEE).
OEE tells you how often and how long machinery experiences unexpected downtime, how frequently faults arise, and what the cost of this downtime or faulty operation is to your productivity in terms of time, volume, and money.
By collecting this data over a longer, consecutive period (min. two weeks), you’ll be able to identify the bottlenecks and their solutions more easily.
Step 5: Identify main losses
If all went to plan, you now know which items of machinery and processes are operating below par and are preventing you from hitting your production targets.
This information forms the basis for making focused performance improvements:
- Put together a multidisciplinary team to solve the foremost problems. In an ideal situation, this team should consist of four to six members (operators, technicians, a qualified supervisor) armed with the highest available expertise, experience, and equipment. Make sure the ‘chemistry’ between individual team members makes for a good mix.
- Schedule structured sessions to solve any outstanding problems. In these sessions, identify the root cause underlying any processes or environments operating below par and determine the best solution available.
- Using your OEE data, you’ll be able to create a useful schedule for fixing the foremost problems affecting productivity.
Step 6: Introduce a proactive maintenance program
Now you know what you need to improve, it’s time to introduce a proactive maintenance program and integrate this with your regular scheduled maintenance program.
Proactive maintenance focuses primarily on the following issues:
- Pay particular attention to fragile systems, machinery, or parts and tooling.
- Keep a logbook documenting the condition of systems, machinery, parts, and tooling after each inspection. This allows you to keep track of wear & tear over time and replace parts in time before this causes a problem.
- Plan a monthly audit to update your logbook and check that scheduled maintenance is on track.
Step 7: Embed TPM
This last step involves embedding TPM firmly into your organization’s standard operating procedures. What’s more, it entails implementing TPM immediately any time you purchase new machinery or equipment, as this will provide you with a benchmark and concrete data to evaluate its efficiency and performance levels in the future.
Tip: present your results visually using a skills matrixCopied
There’s more to do than just implementing TPM. It’s also important to keep track of how effective TPM is being and the progress you’re making, in terms of production and organization. Apply continuous improvement principles to your processes, services, and products – view improvement as a never-ending, incremental process rather than a one-off, large-scale project.
AG5’s skills management software is an ideal tool for visualizing the progress you’re making with TPM. Use internal skills audits to map your organization’s knowledge, skills, and abilities, as these provide you greater clarity about the effect TPM is having.
Skills matrices are the perfect tool for conducting skills audits. Download our sample MS Excel template to get started with skills matrices if you’re not that familiar with them yet.
Unfortunately, Excel spreadsheets and skill matrices don’t play nice together in the long term. Spreadsheets quickly become overly complex, error-prone, and tricky to manage in terms of version control. Staff often edit and share files with one another, and before you know it, no one knows who has the latest version or where they saved it.
Avoid all these pitfalls by using AG5’s software! Update skill set information from the work floor in real time. And forget version conflicts because all your information is stored centrally. It’s the ideal solution for organizations looking to get to grips with their TPM policies.
Find out more or schedule a live demo.
Putting theory into practiceCopied
Implementing TPM successfully relies fully on having a solid step-by-step action plan in place. First, identify where the problems lie and then determine the best solutions. Next, introduce a proactive maintenance program to improve productivity and processes.
If all goes to plan, you’ll soon start noticing you’re experiencing less downtime, fewer productivity fluctuations, and lower maintenance costs!