7 ways to prevent industrial accidents
In this article we discuss effective strategies to prevent industrial accidents, offering insights, tips, and steps to ensure workplace safety and enhance overall organizational well-being.
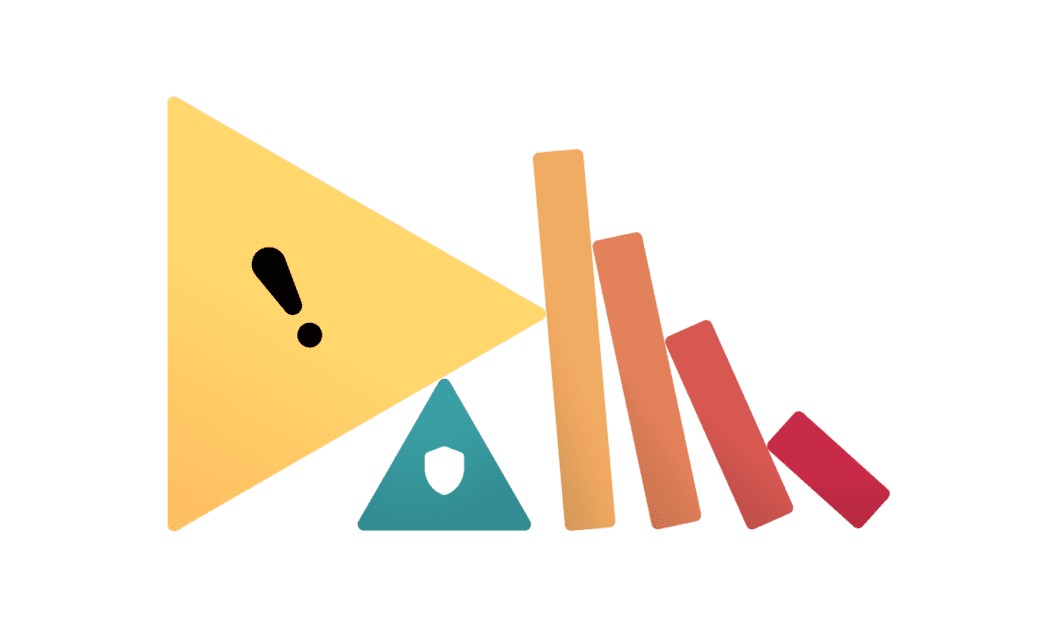
An industrial accident has far-reaching consequences for both employees and their organizations. Not only do they carry serious health and safety implications, but they’re also costly and can lead to production delays.
In this article, we’ll provide you with seven tips you can use to prevent industrial accidents in the workplace. We’ll also explore common causes of industrial accidents, how you can investigate them when they occur – and how AG5 can help you implement a skill-based system in your organization that can raise safety standards, ensure regulatory compliance, and boost productivity.
7 ways to prevent industrial accidentsCopied
Here are seven tips for preventing industrial accidents in the workplace.
1. Create a safety plan
Preventing industrial accidents starts with clear, organization-wide communication regarding health, risk, and safety measures. [1] This plan should encompass risk analysis, hazard identification and management, and incident documentation. Be sure to use clear, simple language and hold frequent team meetings to ensure that everyone stays aligned and vigilant.
2. Clearly mark walkways and roadways
A clear circulation or routing plan is essential to preventing accidents. Clearly mark walkways and roadways, and consider the following carefully, especially in large industrial buildings or warehouses.
When creating such a plan, clearly mark walkways and roadways – and carefully situations such as unloading zones, pedestrian crossings, blind spots, and speed restrictions.
3. Keep the workplace neat and tidy
Discarded packaging, loose cabling, and cluttered passageways are a leading cause of accidents – and have no place in a safe working environment.
This means keeping the workplace neat and tidy is essential. [2] This is an ongoing process – and should be part of all employees’ daily responsibilities.
4. Keep accurate records
Employees with the right skills, qualifications, and certifications to operate machinery, perform certain tasks, and respond to emergencies go a long way toward ensuring safety in the workplace.
This means you’ll need a way to track and manage them. A good tool for this is a skills matrix, which you can initially create as an Excel spreadsheet, before moving to skills management software.
Using AG5’s software, team leaders can enter updates and training results from the shop floor quickly and easily. With the latest versions of their teams’ skills matrices, they can also see who possesses the necessary skills and qualifications to keep the workplace safe. This is perhaps the most important factor in reducing industrial accidents. [3]
5. Ensure personnel availability
Ensuring that your employees with critical safety-related skills and qualifications are on-site is not only crucial for preventing accidents, it also helps you take an adequate and timely response should they occur.
Whether these employees are trained in first aid or full emergency response officers (EROs), employee availability is key here – it’s also an important factor in preventing overworked and overtired staff, itself a large factor in many workplace accidents. [4]
6. Turn data into insight
Data, information, and insight are crucial in preventing accidents and incidents. Thoroughly investigating your organization’s working conditions, processes, and operating procedures can help pinpoint potential risks and hazards, so you can take steps to resolve them. Risk analyses can also allow you preemptively develop safety measures, as well as take action if an accident occurs.
7. Provide personal protective equipment (PPE)
Proper personal protective equipment (PPE) is essential for preventing accidents – and your organization may be legally obligated to provide it to your employees. [4]
PPE could include protective clothing, masks, gloves, helmets, overhead working gear, or ear protection. Always select the best PPE for the job at hand – and ensure that your employees are wearing it.
Common causes of industrial accidentsCopied
In order to take steps to prevent industrial accidents, you’ll need a full understanding of what can cause them. In this section, we’ll take a quick look at several factors that play a big part in many industrial accidents [6]
- Human error. Employee mistakes, such as improper machine operation, ignoring safety procedures, or failing to use personal protective equipment (PPE)
- Mechanical failures. Malfunctioning equipment, machinery breakdowns, or structural failures
- Unsafe working conditions. Poorly maintained facilities, inadequate ventilation, lack of proper lighting, and cluttered workspaces
- Insufficient training. Especially related to equipment use and safety protocols
- Chemical hazards. Exposure to toxic chemicals, gases, or flammable materials
- Electrical hazards. Improper wiring, faulty electrical equipment, or overloading circuits
- Fatigue. Long work hours, shift work, and lack of sufficient rest can impair judgment and reaction times
How to investigate industrial accidentsCopied
In the unfortunate situation that an industrial accident does occur, a prompt and appropriate response is critical. First, you’ll need to attend to anyone who was injured – and potentially contact emergency services, should they be necessary. Then, you’ll need to take steps to properly document the incident. [7]
You can do so by:
- Interviewing those injured, as well as any employees present during the accident
- Analyzing and documenting the scene of the accident, with both photographs and written descriptions
- Taking action to ensure the accident does not reoccur – be it through correcting faulty machinery or unsafe working conditions, or retraining employees who have made mistakes
Ensure workplace safety with AG5Copied
AG5’s skills management software allows you to organize and manage all the components necessary to prevent industrial accidents. With an easy-to-use and intuitive platform and unbreakable skills matrices, you’ll have all the data you need to develop actionable insight into the safety and compliance of your workplace, as well as the well-being of your employees.
With AG5, you can:
- Track and manage safety training progress
- Link employees to the expertise and experience required for jobs, roles, or tasks
- Find suitable replacements for employees off sick
- Set alerts for expiring certifications
- Keep accurate records of all your employees’ skills, qualifications, and certifications
- And much more
Want to see it in action? Schedule a free, live, 15-minute demo for a custom look at how you could use AG5 in your organization.
Sources Copied
- Change view: Table
-
APA
# | Source title | Description | Publication | Retrieved | Source URL |
---|---|---|---|---|---|
1 | 11 Tips for Accident Prevention in the Workplace. | Indeed | August 16, 2024 | December 17, 2024 | https://www.indeed.com/career-.. |
2 | Tips for Accident Prevention in the Workplace. | Tulane University | February 10, 2024 | June 3, 2024 | https://publichealth.tulane.ed.. |
3 | World Day for Safety and Health at Work - Two million work deaths a year: A preventable tragedy. | ILO | April 28, 2004 | June 3, 2024 | https://www.ilo.org/resource/a.. |
4 | 10 Tips to Prevent Workplace Injuries. | Concentra | June 3, 2024 | June 3, 2024 | https://www.concentra.com/reso.. |
5 | 7 Ways to Prevent Workplace Accidents. | The Safety Mag | September 22, 2021 | June 3, 2024 | https://www.thesafetymag.com/c.. |
6 | What Are the Main Causes of Industrial Accidents? | Briotix Health | February 12, 2019 | June 3, 2024 | https://news.briotix.com/what-.. |
7 | How to Conduct an Accident Investigation. | SHRM | June 3, 2024 | June 3, 2024 | https://www.shrm.org/mena/topi.. |
Author Copied
Revisions Copied
Written by: Rick van Echtelt
Copy edited by: Adam Kohut