Customers
Real results achieved by our customers
Read case study
Gary Morrison
Business Services Manager
Our new skills matrices have led to a cultural shift, with everyone saying it's so much better than we had before.
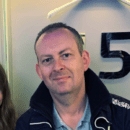
Read case study
Adilson Ferreira
Training Director
Fifteen sites across 11 countries are now using the same language for our Skills program.
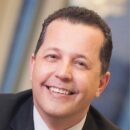
Read case study
Joyce Faustin - van de Ven
Manager Talent Management
Employees provide proof of training with their mandatory digital signature in the AG5 app
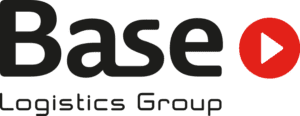
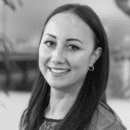
Read case study
Doris Kogler
L&D Specialist
There were 2 big requirements from our production colleagues: the system needs to be user-friendly and we want to see all the data in one place
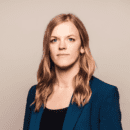
Read case study
Martijn Reijm
Department Head of Primary
We now know exactly what our people are capable of, and that is essential given the massive construction task ahead of us to enable the energy transition
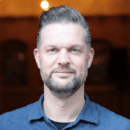
Read case study
Francois van Baal
EHS Training & Compliance Coordinator
It saves a huge amount of work, both for me and for the employees
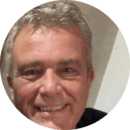
Read case study
Jan Willem ten Barge
Training Coordinator
All skills-related information is now available digitally and in one place
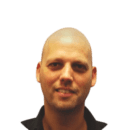
Read case study
Tim Clansey
Training Coordinator
We now use 97% less paper thanks to the elimination of 800 paper documents
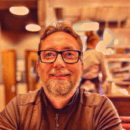
Read case study
Connie Jager
Staff & Organisation
We now have zero stress when the Accreditation Council conducts its monthly audit."
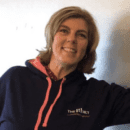
Read case study
John Kanters
Learning & Development Coordinator
We are a typical US company – very data-driven and everything is based on targets.
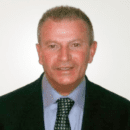
Read case study
Tim Klein Rot
Continuous Improvement Coordinator
Finally! Our skills matrices are now up to date and accurate

Read case study
Rene Burgering
IT Consultant Tatasteel
We’re light years ahead now we’ve gotten rid of Excel!
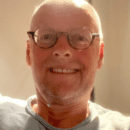
Read case study
Gerard Drost
QHSE Manager at van der Heide
An app with all your certifications at your fingertips!
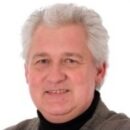
Read case study
Oliver Knaus
Head of IT at BING Power Systems
An amazing tool that’s both pleasing to the eye and pleasant to work with – day in, day out!
Read case study
Danny ten Veen
Coordinating Histology Analyst (LabPON)
Auditors used to have to sift through mountains of paperwork
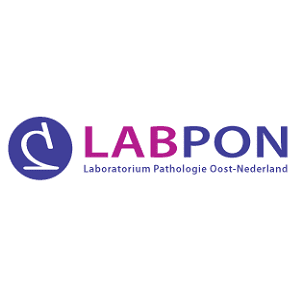
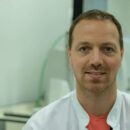
Read case study
Tatiana de Bihl
Training Coordinator at Rogers Corporation
We now have all departments using one tool, and that’s saving me a whole stack of time.
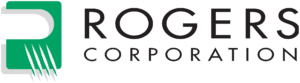
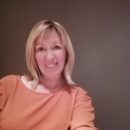
Read case study
Sonja van Dijk
Education & Training Coordinator at Intersnack
You can spot a gap in your staff’s training at a single glance!
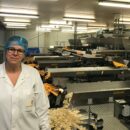
Read case study
Wouter de Smet
Training Coordinator at ArcelorMittal Tailored Blanks Ghent
We used to have to lash four or five different systems together to extract any semblance of an overview
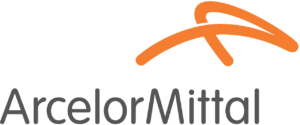
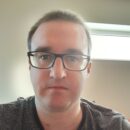
Read case study
Gerard van Moerkerk
Training Coordinator at JDE Coffee
There’s now just one version of each matrix, which is also always up to date
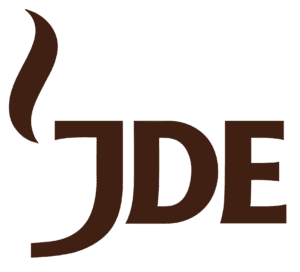
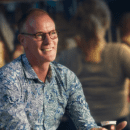
Read case study
Patrick van Dinther
Manager School of Bakery at Cérélia
It takes me one minute to find the info that used to take me a whole day to find!
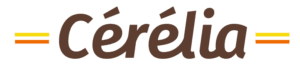
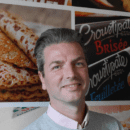
Read case study
Martin Stumpe
Group Lead at Syngenta
We had to dump 480 kg of seed.
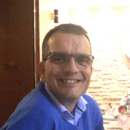
Read case study
Daniel van der Woude
Innovation Manager at Johma
I think it saves us about eight hours a week!
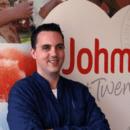
Read case study
Gert Mijnders
Compliance Manager at KLM Cargo
Every month, one organization or another comes to audit us
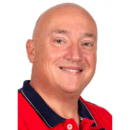
Read case study
Edwin van Spronsen
Program Manager at De Stiho Groep
Our operations manager asked me if I could implement AG5 at another site
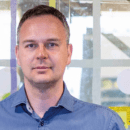
Tired of managing skills in Excel?
Say goodbye to Excel matrices. Start using AG5’s plug and play skill matrix software.
Recognized by G2 for Excellence in Skills Management
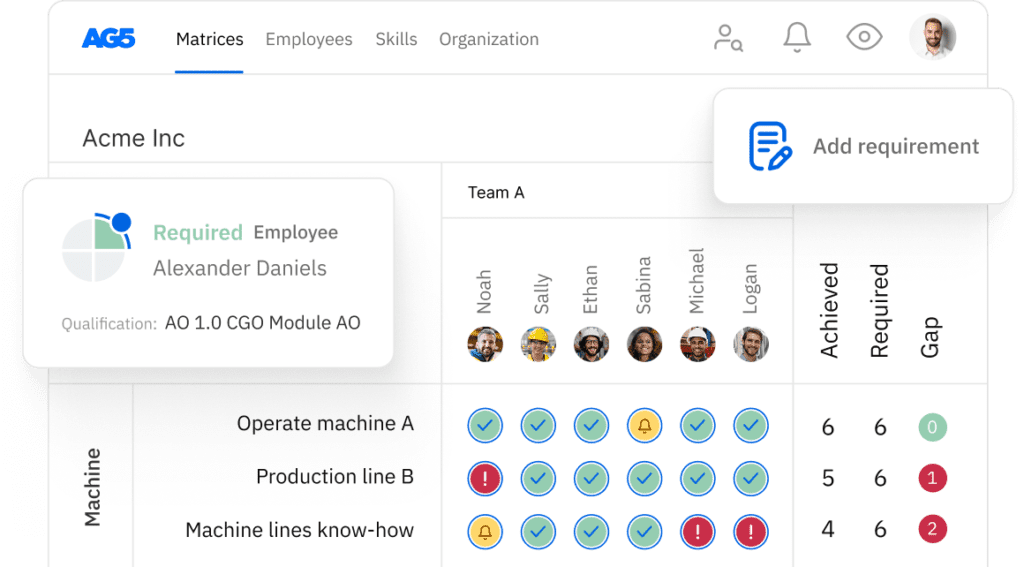