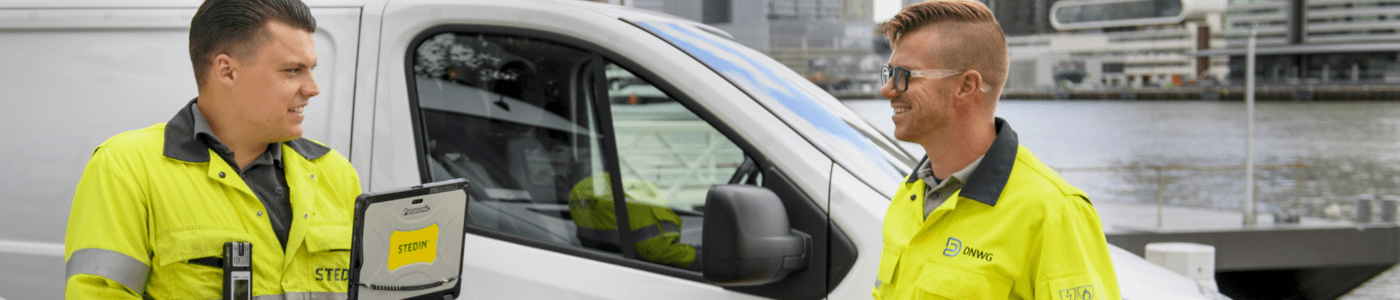
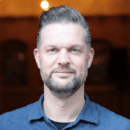
Stedin
Martijn Reijm of Stedin is committed to accurately managing the skills of his team, crucial to the enormous construction challenges posed by the energy transition.
Results achieved:
- Team leaders know the qualifications of the employees. Now they also know what their qualifications enable them to do in terms of the types of tasks, maintenance and projects
- Skills gaps visible for all employees: insight into what employees can do and also what they are not yet able to do
- Error-free reporting on skills thanks to integrations and moving away from Excel
- Knowledge about employee skills no longer disappears when planners change jobs, and instead remains embedded in the system
- In addition to hard skills, soft skills of employees are now also captured
- Employee engagement: in AG5, they can see what other jobs are available and what skills they need for them
- Stedin is working toward a concrete training plan based on AG5’s tooling in order to guide and optimise employee development and growth.
We now know exactly what our people are capable of, and that is essential given the massive construction task ahead of us to enable the energy transition
What were things like previously?
When I joined Stedin, the certificates of the employees were already recorded and findable in a system. But certificates say little about what you are able do: types of tasks, maintenance and projects. It is great that you are listed as competent in high-voltage installations, but does that allow you to do maintenance on an air pressure system? There was no database to show that information.
Planners change frequently and we had to explain every time what people are able to do; very inefficient. Then we discovered AG5, and we were very happy that we didn’t have to go back to maintaining our knowledge competency in Excel. Instead, we have a dedicated tool.
Are things going better now?
Team leaders also did not always know exactly what all their employees could do, because there were skills from previous work experience, for example, that they did not know about. They could often do much more than was recorded. That’s why we redesigned AG5: employees now record their own details in the tool about their experience gained with other employers.
How do you actually use AG5?
For example, I personally directly supervise two chargehands. For those men, I had set up requirements for what they had to be able to do. Then while onboarding, I saw that there were still two skills on red in AG5. So certain skills they should have learned, but they had not learned. The tool makes you aware of the skill gap. Are my people really equipped for the work they are expected to do? That is the difference between AG5 and the way we used to do it in Excel: Excel recorded what skills they had, but not what they did not have. And when a skill is about to expire, AG5 also shows it in due time.
Do you experience any other benefits of AG5?
Employees can now see more things in AG5. I now work in this business unit and I see that super interesting position in that business unit. What do I have to do to get there? Traditionally, an employee would then start in that new position and start learning everything. But in the ideal world, you want the employee to grow toward that learning path from his current position, and then switch when fully qualified and equipped for it. For that reason, team leaders now use AG5 to check the career path with that employee. They go to the staff 4, 5 times a year: let’s take another look in AG5 to see where you stand now. And what’s also nice: you can click on those two features and see the relevant gap analysis at a glance, that is, the skills the employee still needs to learn for that.
What challenges do you have within Stedin?
The energy transition is the biggest rebuild of our energy system ever. We need to invest billions to expand the power grid, and our workload is increasing dramatically. This requires quite a few soft skills from our people in addition to hard skills. We are going to outsource a lot more when experiencing high workloads, and then we are going to check the quality of whoever we awarded the contract. It makes a huge difference whether we make the final connection ourselves, or do a quality check that the contractor completed the end connection to a satisfactory standard. That’s a whole different skill set. It makes quite a difference whether you and your contractor review the contract together to see if the design requirements have been realised, or you create the design requirements yourself. That’s another form of collaboration, and this is a major focus in partnerships. Positions need to be created for this purpose, and again, we enter them into AG5 with their own skill sets.
How do you use AG5 in this challenge?
To each position we add in AG5, we also assign the soft skills required. For example, if a new employee comes in as an apprentice and has no learning ability, then he should not stay with us, because they need to learn a lot, very quickly. If you are a senior specialist and do not have the soft skill that you can teach young people easily, you will not be promoted to that position either.
We now know the exact skill gap of our people. That is essential given the massive construction task ahead of us to enable the energy transition Because knowing what employees can do and what they cannot yet do, enables us to make an accurate workforce planning for the future.
Tired of managing skills in Excel?
Say goodbye to Excel matrices. Start using AG5’s plug and play skill matrix software.
Recognized by G2 for Excellence in Skills Management
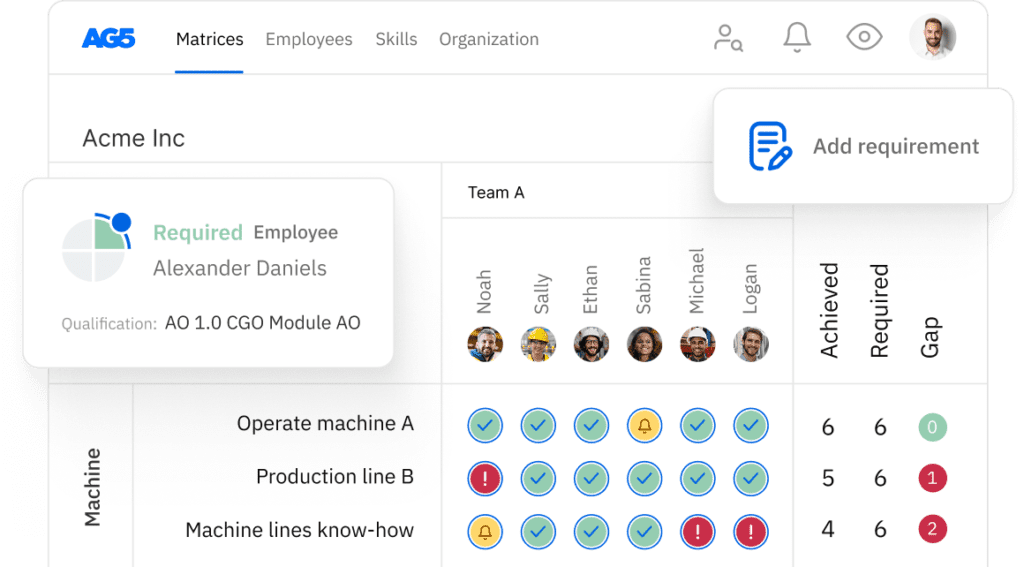