Erfolgreiche Einführung von Total Productive Maintenance (TPM): 7 Schritte
Total Productive Maintenance (TPM) hilft Ihnen dabei, Ihre Maschinen und Anlagen in einem zuverlässigen Zustand zu erhalten. Aber wie sieht ein TPM-Implementierungsplan in der Praxis aus? Und welche Schritte sollten Sie unternehmen, um diese Methodik in Ihre bestehenden Betriebs- und Wartungsverfahren zu integrieren? Lesen Sie hier mehr. Wir zeigen Ihnen, was, wie und warum! Was ist TPM? TPM hat...
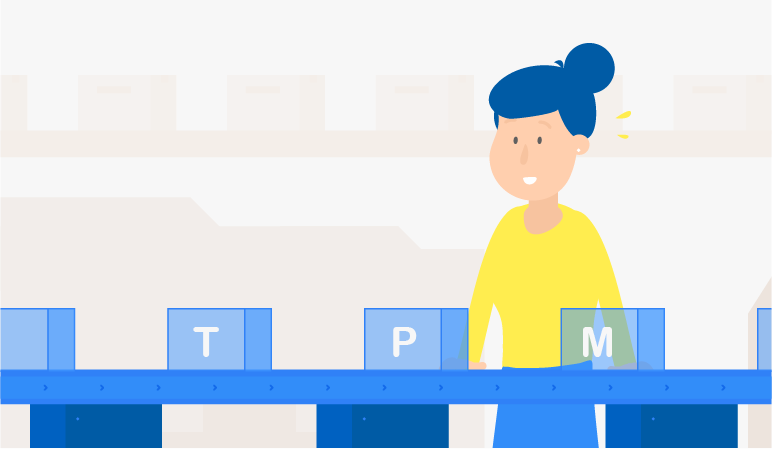
Total Productive Maintenance (TPM) hilft Ihnen dabei, Ihre Maschinen und Anlagen in einem zuverlässigen Zustand zu erhalten. Aber wie sieht ein TPM-Implementierungsplan in der Praxis aus? Und welche Schritte sollten Sie unternehmen, um diese Methodik in Ihre bestehenden Betriebs- und Wartungsverfahren zu integrieren?
Lesen Sie hier mehr. Wir zeigen Ihnen, was, wie und warum!
Was ist TPM?Copied
TPM hat seinen Ursprung in der japanischen Industrie und trägt zur Erhaltung und Verbesserung der Produktionssysteme bei. TPM ist ein umfassendes Konzept, bei dem alle Mitarbeiter auf allen Ebenen in die Wartung und Instandhaltung der Anlagen und Maschinen ihres Unternehmens miteinbezogen werden.
Die richtige Anwendung der Prinzipien hilft Ihnen, die Wahrscheinlichkeit von Geräteausfällen zu minimieren und die Produktivität und Kontinuität zu maximieren. Außerdem trägt TPM dazu bei, das Bewusstsein der Mitarbeiter für Technologie, Sicherheit und Umwelt zu schärfen, weil sie ein Gefühl der Verantwortung für die Geräte und Maschinen bekommen, mit denen sie täglich arbeiten.
TPM besteht aus acht Säulen:
- Gezielte Verbesserung
- Autonome Wartung
- Geplante Wartung
- Frühzeitige Verwaltung von Geräten/Produkten
- Bildung und Ausbildung
- Qualitätsmanagement
- Gesundheit, Sicherheit und Umwelt (Health, Safety & Environment /HSE)
- Verwaltung und Büro
Mehr dazu erfahren Sie in unserem Artikel „Was ist TPM?“.
Schritt für Schritt zum erfolgreichen TPMCopied
Aber wie sollten Sie TPM in der Praxis umsetzen? Das erklären wir Ihnen in den nachfolgenden Schritten.
Schritt 1: Teilen Sie Ihre Pläne mit Ihrer gesamten Organisation
TPM funktioniert nur, wenn alle Mitarbeiter in Ihrem Unternehmen die Hauptziele und den Wert, den es mit sich bringt, verstehen. Vor allem aber ist es wichtig, dass Management und Vorgesetzte die Bedeutung ordnungsgemäßer TPM-Verfahren begreifen. Wenn Führungskräfte eine bestimmte Arbeitsweise anpreisen, einführen und praktizieren, werden die Mitarbeiter in den Betrieben die Pläne im Allgemeinen viel schneller annehmen.
Schritt 2: Identifizieren Sie geeignete Systeme, Maschinen oder Verfahren
Schritt 2 besteht darin, einen geeigneten Bereich in Ihrer Arbeitsumgebung zu finden, in dem Sie einen TPM-Pilotversuch durchführen können. Dabei kann es sich um ein bestimmtes Gerät, ein System oder sogar um einen Teil eines Produktionsprozesses handeln, der nicht so reibungslos läuft.
Finden Sie heraus, welche Elemente Ihnen einen schnellen Gewinn bringen würden. Die SMART-Methode ist ein nützliches Mittel, um diese Auswahl zu treffen. SMART steht für „Specific, Measurable, Achievable, Realistic, Time-related“ (spezifisch, messbar, erreichbar, realistisch und zeitbezogen).
Schritt 3: Versetzen Sie Ihre Systeme in einen optimalen Betriebszustand
Zu Schritt 3 gehört der Start Ihres Pilotversuchs. Definieren Sie die Parameter, die die in Schritt 2 ermittelten Systeme oder Prozesse erfüllen sollen. Das 5S-System ist hierfür ein nützliches Instrument, da es Sie zwingt, die angestrebten Verbesserungen zu definieren. 5S steht für „Sort, Set, Shine, Standardize, Sustain“ (sortieren, einstellen, glänzen, standardisieren, aufrechterhalten).
Beginnen Sie damit, Fotos von der „alten Situation“ zu machen.
Räumen Sie dann den Arbeitsbereich auf, und entfernen Sie alle herumliegenden Ersatzteile und Werkzeuge. Reinigen Sie jetzt alle Maschinen und Geräte, und machen Sie ein Foto des Arbeitsplatzes in der „neuen Situation“. Anhand von Kontrollen können Sie feststellen, ob die Mitarbeiter ihre Arbeitsplätze langfristig sauber halten.
Jetzt, wo Sie ein klareres Bild von den Geräten und Maschinen und ihrem aktuellen Zustand haben, können Sie mit der Ausarbeitung eines autonomen Wartungsplans beginnen. In diesem Plan ist genau festgelegt, wie Sie Ihre Maschinen und Ihren Arbeitsplatz instand halten und wer was und wann tun muss.
Schritt 4: Messen Sie die Gesamteffektivität der Systeme
In Schritt 4 geht es um die Messung und Erfassung von Daten, damit Sie mit der Schaffung einer optimal gestalteten und effizienten Produktionsumgebung beginnen können. Der beste Weg dafür ist die Verwendung des Konzepts der Gesamtanlageneffektivität (Overall Equipment Effectiveness/OEE).
Die OEE gibt Aufschluss darüber, wie oft und wie lange Maschinen unerwartete Ausfallzeiten haben, wie häufig Fehler auftreten und wie hoch die Kosten dieser Ausfallzeiten oder fehlerhaften Betriebsabläufe für Ihre Produktivität in Form von Zeit, Volumen und Geld sind.
Wenn Sie diese Daten über einen längeren, zusammenhängenden Zeitraum (mindestens zwei Wochen) sammeln, können Sie die Engpässe und ihre Lösungen leichter erkennen.
Schritt 5: Ermitteln Sie die Hauptverluste
Wenn alles nach Plan gelaufen ist, wissen Sie jetzt, welche Maschinen und Prozesse unzureichend funktionieren und Sie daran hindern, Ihre Produktionsziele zu erreichen.
Diese Informationen bilden die Grundlage für gezielte Leistungsverbesserungen:
- Stellen Sie ein multidisziplinäres Team zusammen, um die wichtigsten Probleme zu lösen. Im Idealfall sollte dieses Team aus vier bis sechs Mitgliedern (Bedienern, Technikern, einem qualifizierten Aufseher) bestehen, die über die bestmöglichen Fachkenntnisse, Erfahrungen und Ausrüstungen verfügen. Achten Sie darauf, dass die „Chemie“ zwischen den einzelnen Teammitgliedern stimmt.
- Planen Sie strukturierte Sitzungen, um offene Probleme zu lösen. In diesen Sitzungen werden die Grundursachen für unzureichend funktionierende Prozesse oder Umgebungen ermittelt und die beste verfügbare Lösung bestimmt.
- Mithilfe Ihrer OEE-Daten können Sie einen nützlichen Zeitplan für die Behebung der wichtigsten Probleme erstellen, die die Produktivität beeinträchtigen.
Schritt 6: Führen Sie ein proaktives Wartungsprogramm ein
Jetzt, wo Sie wissen, was Sie verbessern müssen, sollten Sie ein proaktives Wartungsprogramm einführen und in Ihr reguläres Wartungsprogramm integrieren.
Die proaktive Wartung konzentriert sich vor allem auf folgende Punkte:
- Achten Sie besonders auf empfindliche Systeme, Maschinen oder Teile und Werkzeuge.
- Führen Sie ein Logbuch, in dem Sie den Zustand von Systemen, Maschinen, Teilen und Werkzeugen nach jeder Inspektion dokumentieren. So können Sie die Abnutzung im Lauf der Zeit verfolgen und Teile rechtzeitig austauschen, bevor sie ein Problem verursachen.
- Planen Sie ein monatliches Audit, um Ihr Logbuch zu aktualisieren und zu prüfen, ob die geplanten Wartungsarbeiten durchgeführt werden.
Schritt 7: Integrieren Sie TPM
Dieser letzte Schritt beinhaltet die feste TMP-Verankerung in die Standardbetriebsverfahren Ihres Unternehmens. Außerdem müssen Sie TPM bei jeder Neuanschaffung von Maschinen oder Anlagen sofort einführen, da Sie auf diese Weise einen Richtwert und konkrete Daten erhalten, um die Effizienz und das Leistungsniveau in Zukunft zu bewerten.
Tipp: Stellen Sie Ihre Ergebnisse mithilfe einer Qualifikationsmatrix visuell darCopied
Es gibt mehr zu tun als nur TPM einzuführen. Es ist auch wichtig, dass Sie die Effektivität von TPM und die Fortschritte in den Bereichen Produktion und Organisation verfolgen. Wenden Sie die Grundsätze der kontinuierlichen Verbesserung auf Ihre Prozesse, Dienstleistungen und Produkte an. Betrachten Sie die Verbesserung als einen nie endenden, schrittweisen Prozess und nicht als ein einmaliges, großangelegtes Projekt.
Die Kompetenzverwaltungssoftware von AG5 ist ein ideales Instrument, um Ihre TPM-Fortschritte zu visualisieren. Nutzen Sie interne Qualifikationsprüfungen, um die Kenntnisse, Fähigkeiten und Fertigkeiten innerhalb Ihrer Organisation zu erfassen, da diese Ihnen mehr Klarheit über die Wirkung von TPM verschaffen.
Qualifikationsmatrizen sind das perfekte Instrument für die Durchführung von Qualifikationsprüfungen. Laden Sie sich unsere MS Excel-Mustervorlage herunter, um das Arbeiten mit Qualifikationsmatrizen zu beginnen, wenn Sie noch nicht so vertraut damit sind.
Leider vertragen sich Excel-Tabellen und Qualifikationsmatrizen auf Dauer nicht gut. Tabellenkalkulationen werden schnell zu komplex und fehleranfällig, und die Versionskontrolle lässt sich nur schwierig verwalten. Mitarbeiter bearbeiten häufig Dateien und tauschen sie untereinander aus. Und ehe man sich versieht, weiß niemand mehr, wer die neueste Version hat oder wo sie gespeichert wurde.
Vermeiden Sie all diese Fallstricke, indem Sie die Software von AG5 verwenden! Aktualisieren Sie die Qualifikationsdaten am Arbeitsplatz in Echtzeit. Und vergessen Sie Versionskonflikte, weil alle Ihre Informationen zentral gespeichert werden. AG5 ist die ideale Lösung für Unternehmen, die ihre TPM-Richtlinien in den Griff bekommen möchten.
Erfahren Sie mehr, oder vereinbaren Sie einen Termin für eine Live-Demo.
Copied
Umsetzung der Theorie in die PraxisCopied
Die erfolgreiche TPM-Umsetzung hängt in vollem Umfang von einem soliden, schrittweisen Aktionsplan ab. Ermitteln Sie zunächst, wo die Probleme liegen, und bestimmen Sie dann die besten Lösungen. Führen Sie als Nächstes ein proaktives Wartungsprogramm ein, um Produktivität und Betriebsabläufe zu verbessern.
Wenn alles nach Plan läuft, werden Sie bald feststellen, dass Sie weniger Ausfallzeiten, weniger Produktivitätsschwankungen und geringere Wartungskosten haben!