Total productive maintenance (TPM) succesvol implementeren in 7 stappen
Leer alles over Total Productive Maintenance (TPM) met ons stappenplan voor efficiënte productieprocessen en minimalisering van verspilling.
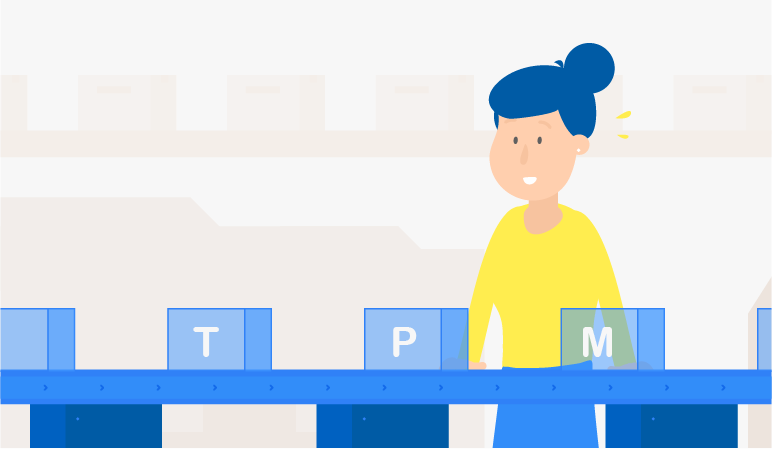
Total productive maintenance (TPM) maakt machineparken betrouwbaar en optimaliseert productieprocessen. Maar hoe kun je TPM implementeren in de praktijk? Welke stappen moet je doorlopen om de werkwijze succesvol te integreren in je bedrijfs- en onderhoudsprocessen? Wij laten het je zien.
Wat is Total Productive Maintenance (TPM)?Copied
Het idee achter TPM is afkomstig uit het Japanse bedrijfsleven. De methodiek streeft vooral naar het onderhouden en verbeteren van productiesystemen. TPM is breed van opzet en streeft naar betrokkenheid van alle medewerkers bij het onderhouden van installaties en machines.
Het goed toepassen van de werkwijze verkleint de kans op machine-uitval, waardoor processen continu door kunnen draaien en de productie op peil blijft. Bovendien zorgt TPM voor bewustzijn onder medewerkers op het gebied van techniek, veiligheid en milieu omdat werknemers ownership krijgen over de machines en apparaten waarmee ze werken.
Dit zijn de acht pilaren die de basis vormen van total productive maintenance:
- Gericht verbeteren
- Autonoom onderhoud
- Gepland onderhoud
- Early management
- Opleiding en training
- Kwaliteitsmanagement
- Veiligheid, gezondheid en werkomgeving
- TPM op kantoor
Meer weten? Lees ons artikel ‘Wat is TPM?’ voor meer achtergrondinformatie.
Stappenplan om TPM te implementerenCopied
Maar hoe breng je TPM nu concreet in de praktijk. We leggen het je uit door middel van onderstaand stappenplan.
Stap 1: Deel je plannen met de hele organisatie
TPM werkt alleen als iedereen binnen de organisatie begrijpt wat de hoofddoelen en meerwaarde van de werkwijze zijn. Het is vooral belangrijk om het management en het leidinggevend personeel te doordringen van het belang van een solide TPM-traject. Als managers een werkwijze promoten, uitleggen en adopteren, wordt zo’n plan meestal sneller omarmd door de productiemedewerkers op de fabrieksvloer.
Stap 2: Geschikte installaties, machines of processen identificeren
De tweede stap is het identificeren van een geschikt onderdeel van de werkomgeving waar je de TPO-methode in pilotvorm op kunt loslaten. Dat kan een bepaalde machine of installatie zijn, maar ook een niet-optimaal lopend (onderdeel van een) productieproces.
Kijk vooral naar onderdelen waar je snelle winst kunt boeken. De SMART-methode is een handig hulpmiddel om dit selectieproces vorm te geven. SMART maakt doelen namelijk specifiek, meetbaar, haalbaar, realistisch en planbaar in tijd en ruimte.
Stap 3: Apparatuur in optimale bedrijfstoestand brengen
In deze fase ga je concreet aan de slag met het pilotproject. Stel allereerst een uitgangswaarde vast waar de (in stap 2) geïdentificeerde apparaten of processen aan moeten voldoen. Het 5S-programma (sorteren, schikken, schoonmaken, standaardiseren en systematiseren) is een goed hulpmiddel voor het uitvoeren van deze taak omdat je het verbeterproces er concreet mee vastlegt.
Begin met het maken van foto’s van de ‘oude situatie’.
Vervolgens neem je de werkomgeving flink onder handen: verwijder rommel, overbodige componenten en ongebruikt gereedschap. Maak vervolgens de machines schoon en maak een foto van de werkplek ‘nieuwe stijl’. Aan de hand van audits kun je vervolgens nagaan of de werkplek ook op de lange termijn opgeruimd, schoon en netjes blijft.
Nu je een goed beeld hebt van de apparatuur en de optimale bedrijfstoestand, kun je een goed programma voor autonomous maintenance formuleren. Zo’n plan zorgt voor een structureel onderhoud van machineparken en werkplekken en maakt precies duidelijk welke taken en verantwoordelijkheden individuele medewerkers hebben.
Stap 4: Overall equipment effectiveness (OEE) meten
De volgende stap op weg naar een optimaal ingerichte en efficiënte productieomgeving is meten en data verzamelen. De beste manier om dit te doen is kijken naar de overall equipment effectiveness (OEE).
De OEE laat zien hoe vaak en hoelang machines ongepland stil staan, hoe vaak er defecten optreden en wat stilstaande of niet-optimaal functionerende machines je kosten aan productie (uren en volume) en geld.
Door die data over een langere, aaneengesloten periode (minimaal twee weken) te verzamelen, krijg je meer zicht op knelpunten en oplossingen.
Stap 5: Belangrijke verliespunten identificeren
Als het goed is weet je nu welke machines en processen qua performance achterblijven bij de productiedoelen die je als bedrijf hebt opgesteld.
Die informatie vormt een goede basis voor een project van focus improvement dat prestatieproblemen op diverse manieren aanpakt.
- Creëer een cross-functioneel team dat de belangrijkste problemen oplost. Zo’n team bestaat idealiter uit vier tot zes mensen (operators, monteurs, een deskundige supervisor) die beschikken over een hoog kennisniveau en de beste onderhoudsapparatuur. Let er ook op dat de chemie tussen de afzonderlijke teamleden goed is.
- Organiseer gestructureerde sessies om problemen op te lossen. Tijdens deze bijeenkomsten identificeer je de oorzaken achter matig functionerende productieprocessen en -omgevingen en identificeer je de beste oplossingen voor deze euvels.
- Dankzij de OEE-informatie kun je een goed schema ontwerpen voor het fixen van de problemen die je productie nadelig beïnvloeden.
Stap 6: Proactieve onderhoudstechnieken implementeren
Nu je weet waar en hoe het beter moet, kun je proactieve onderhoudstechnieken gaan integreren in het reguliere onderhoudsprogramma.
Dit proactieve onderhoud richt zich vooral op de onderstaande aandachtspunten.
- Besteed extra aandacht aan de kwetsbaarste installaties, machines en machineonderdelen.
- Leg de toestand van installaties, machines en onderdelen na inspectie vast in een logboek. Zo kun je over een langere periode bijhouden hoe het zit met de slijtage en kun je onderdelen van machines vervangen voordat wear-en-tear een probleem wordt dat de productie beïnvloedt.
- Plan een maandelijkse onderhoudsaudit waarin je het logboek bijwerkt en verifieert dat het geplande onderhoudsschema is gevolgd.
Stap 7: Maak van TPM een blijvertje
De laatste stap: zorg ervoor dat TPM een blijvertje wordt binnen de organisatie. Dit betekent dat de werkwijze een vast onderdeel gaat vormen van de bedrijfscultuur, en dus ook bij de aanschaf van nieuwe machines en installaties gelijk wordt toegepast om de efficiëntie en performance van die nieuwe apparatuur in concrete cijfers te vangen.
Tip: maak de resultaten zichtbaar met een skills matrixCopied
Met alleen het implementeren van TPM ben je er nog niet. Het is ook belangrijk om bij te houden hoe succesvol de werkwijze is en wat de voortgang is die je op organisatorisch en productioneel vlak maakt. Ga daarbij uit van het principe van continuous improvement: het verbeteren van processen, diensten en producten is een doorlopende inspanning in plaats van een eenmalige zaak.
De skills management software van AG5 is een tool die uitstekend van pas komt bij het inzichtelijk maken en houden van het TPM-proces. De interne skills audit, die gericht is op het in kaart brengen van de kennis, vaardigheden en competenties die binnen je organisatie voorhanden zijn, is een werkwijze die je inzicht geeft in het succes van total productive maintenance.
De belangrijkste tool voor het uitvoeren van een skills audit is de skills matrix. Als je nog weinig ervaring hebt met dit stukje gereedschap, kun je beginnen in Excel, bijvoorbeeld door dit voorbeeldtemplate als uitgangspunt te nemen.
Helaas zijn Excel en de skills matrix geen ideale combinatie. Excel-matrixen zijn vaak complex, foutgevoelig en tricky op het vlak van versiebeheer. De bestanden worden vaak door meerdere mensen gebruikt, bijgewerkt en vervolgens binnen de organisatie rondgestuurd. Na verloop van tijd ontstaat zo onduidelijkheid over wie nu op enig moment met welke versie werkt.
De software van AG5 biedt uitkomst. Skillsets zijn snel en direct op de werkvloer bij te werken. Omdat alle informatie raadpleegbaar is vanuit één centrale omgeving, heb je ook niet te maken met complicaties op het gebied van versiebeheer. Dé oplossing dus voor organisaties die structuur willen aanbrengen in hun TPM-beleid! Lees hier hoe het werkt of vraag meteen een live demo aan.
Vertaal de theorie naar de praktijkCopied
Het succesvol implementeren van TPM valt of staat met een degelijk en goed gestructureerd stappenplan. Zoek eerst uit waar de problemen zitten en hoe je die het beste kunt oplossen. Vervolgens kun je concreet aan de slag gaan en met een proactief onderhoudsbeleid productiemiddelen en -processen verbeteren. Het resultaat: minder downtime, minder productieschommelingen en lagere onderhoudskosten!