Operational excellence definition: A simple guide
In this article, we discuss the definition of operational excellence. It provides a simple guide to understanding the concept and its importance in achieving organizational success and efficiency.
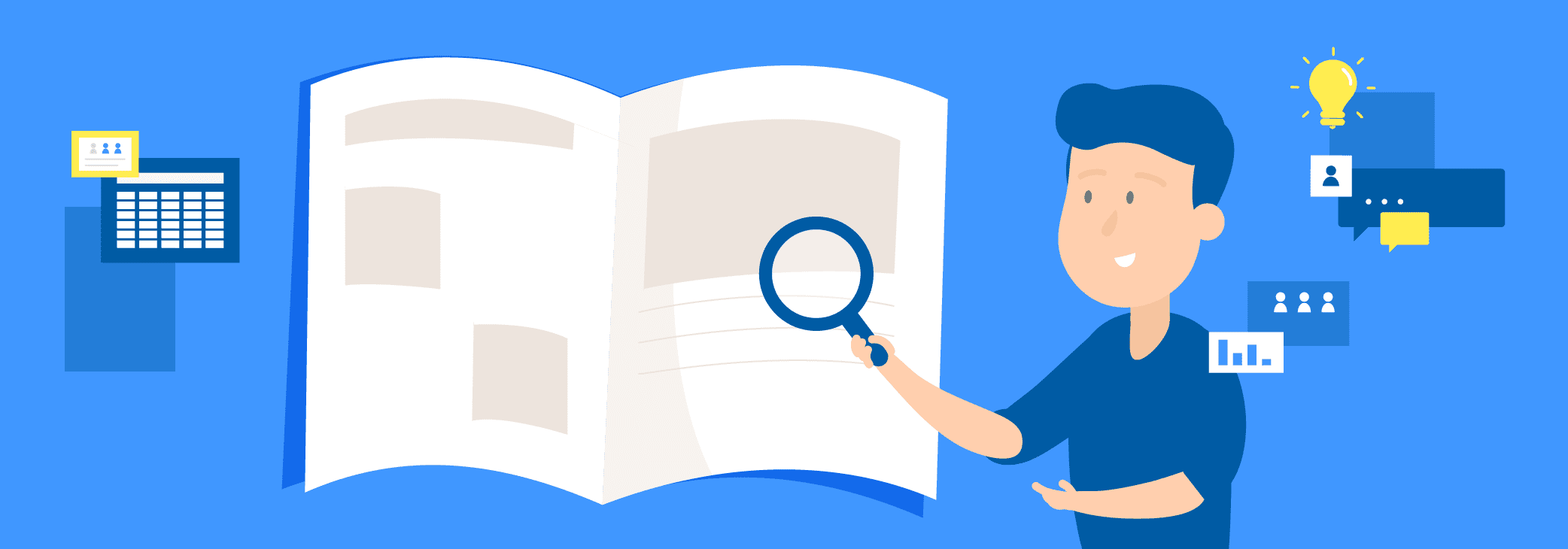
Operational excellence is a principle that can be applied at all levels of an organization, from the front lines to the C-suite. Setting and achieving ambitious goals and looking for ways to improve continuously may sound like common sense, but an incredible number of organizations lose sight of this simple truth in the day-to-day grind. Operational excellence is the continuous and deliberate pursuit of improved performance. This article takes a close look at the operational excellence definition. We explore:
By the end of this article, you’ll have a better understanding of how operational excellence can help your organization reach new levels of success.
What is operational excellence?Copied
In definition, operational excellence is a business philosophy that stresses the importance of continuously improving operations.
It aims to minimize waste, optimize processes, and deliver customer value.
Companies that wish to achieve operational excellence must first identify areas for improvement and then take action to improve those areas.
It’s a journey, not a destination, and it requires commitment from everyone in the organization.
When businesses employ operational excellence, they create a culture of continuous improvement that benefits everyone in the organization and a competitive advantage that leads to long-term success.
Operational excellence can be achieved by implementing lean management principles that can be combined with the Six Sigma methodology, or other process improvement initiatives. However, it’s about striving for improvement rather than perfection.
What is the operational excellence framework?Copied
The operational excellence framework is a set of guidelines designed to help organizations achieve operational excellence.
The framework’s four pillars are strategy development, performance management, leadership and culture, and process excellence.
The first pillar (strategy development) refers to businesses having clear and achievable visions for their operational excellence journeys, such as reducing waste, improving customer satisfaction, or increasing profitability.
Once a business has established its goals, it must develop a plan for achieving them based on a solid understanding of its current state and future objectives.
The second pillar (performance management) signifies measuring progress and making adjustments to ensure businesses are on track to meet their objectives.
This can involve tracking key performance indicators, conducting regular audits, or implementing continuous improvement programs.
The third pillar (leadership and culture) represents businesses having the correct people to support their operational excellence journeys.
This might involve developing or improving employee training programs, establishing mentorship programs, or creating incentives to encourage employees to embrace continuous improvement.
The fourth pillar (process excellence) denotes ensuring businesses have efficient and effective processes, which may involve streamlining manufacturing processes, improving customer service procedures, or implementing lean principles across organizations.
What are the operational excellence methodologies?Copied
There are numerous operational excellence methodologies, but the most popular are Six Sigma and lean manufacturing:
- Six Sigma is a methodology that focuses on improving quality by reducing defects. It uses tools and techniques to identify and eliminate waste in processes. Businesses must train their employees in Six Sigma methodology and provide them with the resources they need to succeed.
- Lean manufacturing is a methodology for eliminating waste in processes. It is based on continuous improvement and is often used in conjunction with Six Sigma. Businesses must train their employees in lean manufacturing methodology and provide them with the resources they need to succeed.
The two approaches are complementary and combined they are used as a data-driven process called Lean Six Sigma.
What are the operational excellence principles?Copied
In definition, operational excellence principles are guidelines for improving companies’ operations and cultures.
Businesses that adhere to these principles can foster a culture of continuous improvement that benefits everyone in those organizations.
There are many models and principles for Operational Excellence such as Kaizen and the Shingo Model, both originating in Japan.
The 5 principles of Kaizen are: Know your Customer, Let it Flow, Go to Gemba, Empower People and Be Transparent.
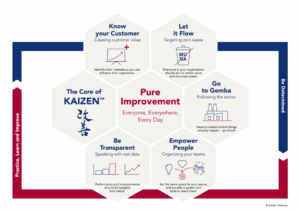
The Shingo Model’s principles are as follows:
- Lead with humility: Leaders should be humble and always willing to learn from others.
- Respect everyone: Employees should be treated with respect and allowed to contribute to the organization’s success.
- Focus on the process: Businesses should focus on improving their operations, not just their bottom lines.
- Embrace scientific thinking: Businesses should use data and analytics to drive their decision-making.
- Flow and pull value: Businesses should deliver value to customers while minimizing waste.
- Assure quality at the source: Businesses should strive to produce high-quality products and services.
- Seek perfection: Businesses should strive to be better, even if they never reach perfection.
- Create a clear purpose: Businesses should have a clear and achievable vision for their future.
- Think systemically: Leaders should view operations as part of a more extensive system.
- Create value: Leaders should focus on delivering value to customers and employees. Shareholders are important, but you don’t have a business without customers or employees.
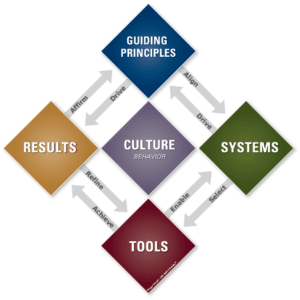
The challenges organizations face when implementing operational excellenceCopied
Operational excellence is a crucial business philosophy that emphasizes the need for organizations to constantly strive to improve their performance.
However, implementing operational excellence can be difficult because it necessitates a paradigm shift in many traditional businesses’ thinking and culture.
Organizations face several challenges when attempting to operationalize excellence:
- Reducing top-down thinking: Decision-making is top-down in many organizations, with a small group of senior leaders making all the decisions. Employees may feel that their ideas are not valued or listened to further up the hierarchy, which can stifle creativity and innovation. To operationalize excellence, organizations must encourage a more open and collaborative approach to decision-making, involving employees at all levels.
- Detachment: Operational excellence emphasizes the need to be constantly aware of and responsive to changes in the external environment. However, some organizations become overly focused on their internal operations and lose sight of what is happening outside. As a result, they may miss opportunities or be blindsided by market changes. To avoid this, organizations must have systems and processes to monitor their external environments and identify potential changes that could impact their businesses.
- Lack of progress: Since operational excellence is an ongoing journey, organizations must be prepared for results to take time and effort. They need patience, tenacity, and a willingness to invest in long-term change to succeed. Some organizations become frustrated and give up too soon when they don’t see immediate improvements.
- Lack of willingness to adapt: Operational excellence requires organizations to be flexible and adaptable, as they must constantly learn and evolve to stay ahead of the competition. However, some organizations resist change and prefer to maintain the status quo. To operationalize excellence, they must create cultures of learning and innovation in which employees feel comfortable trying new things and taking risks.
- Overly complex data: In today’s data-driven world, organizations often collect vast amounts of information about their operations. However, this data can be overwhelming and challenging to process. To operationalize excellence, organizations must invest in systems and tools that help them make sense of their data and use it to drive decision-making.
How to achieve operational excellenceCopied
Now you learned about the operational excellence definition and how to use it in business.
But how to achieve it? Although each organization’s path to excellence is unique, there are seven general principles to follow to reach operational excellence:
- Set clear goals and objectives: Setting clear goals and objectives is the first step toward excellence. What does your organization want to achieve? How will you know when you’ve completed it? It will be difficult to measure progress or identify areas for improvement unless you have a clear idea of what you are trying to achieve.
- Involve employees at all levels: It’s essential to involve employees at all levels in the process because operational excellence requires a shift in thinking and culture. This will help ensure that everyone is on board with the changes and understands what they need to do to contribute to the organization’s success.
- Simplify processes: Simplification is one of the critical principles of operational excellence. Complex processes can be a significant barrier to excellence, leading to errors and delays. Therefore, organizations must streamline their processes and remove unnecessary steps.
- Automate where possible: Another way to simplify processes is to automate them. This can help reduce errors and give employees more time to focus on value-added tasks.
- Promote a culture of learning and innovation: As operational excellence requires a continuous improvement mindset, an organization must promote a culture of learning and innovation that encourages employees to experiment, take risks, and learn from mistakes.
- Use data to drive decision-making: Data is a powerful tool that can help organizations achieve operational excellence. Organizations can identify improvement areas and make decisions based on evidence rather than guesswork by collecting and analyzing data.
- Continuously measure and monitor progress: To operationalize excellence, organizations must continuously measure and monitor their progress. This will help them identify areas where they are making progress and where they need to continue to focus their efforts.
There is no one-size-fits-all solution to achieving operational excellence. However, any organization can operationalize excellence and reap the benefits of improved performance by following the principles of simplification, automation, data-driven decision-making, and continuous improvement. We hope this guide about Operational excellence definition, principles, and benefits has been helpful to you.
Improve operational excellence with AG5 skills management softwareCopied
AG5 Software is an excellent tool for any organization striving to employ operational excellence.
It helps simplify and automate HR processes, which frees time for employees to focus on more value-added tasks.
In addition, AG5 provides extensive data and analytics capabilities that can help organizations drive decision-making and measure progress.
Request a demo today to learn how AG5 can help your organization operationalize excellence.
Use AG5 to identify skill gaps
Say goodbye to Excel matrices. Start using AG5’s plug and play skill matrix software.
ISO27001 certified
Start your 14-day free trial