Process deviation handling skills matrix template
A skills matrix template is a tool teams can use to assess their process deviation handling skills and knowledge
Download your free template here
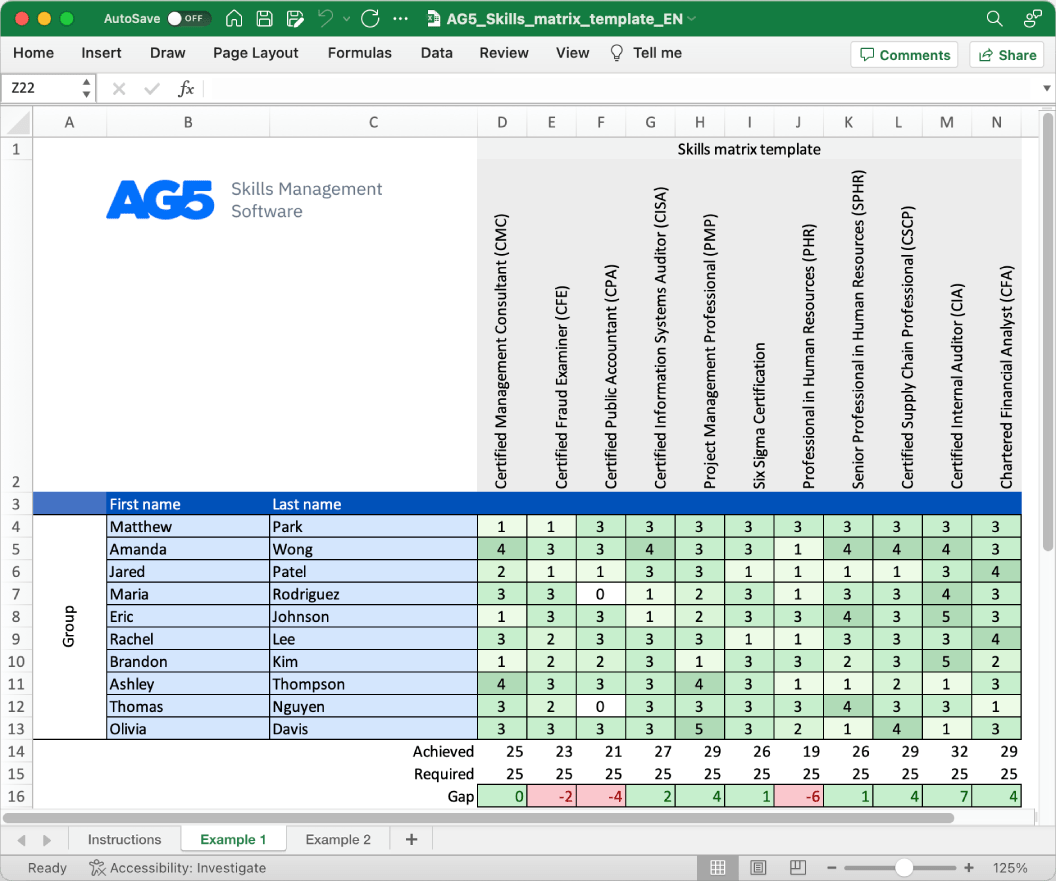
Overview Copied
With our free process deviation handling skills matrix template, you will receive a clear overview of the skills that are present in your organization, as well as those that are missing. Using this information, you can develop and implement a plan to ensure that your employees’ skills are up to date, comprehensive, compliant, and ready for the future.
- Certified Deviation Handling Professional (CDHP)
- Certified Process Deviation Investigator (CPDI)
- Certified Deviation Management Specialist (CDMS)
- Certified Deviation Analyst (CDA)
- Certified Process Deviation Coordinator (CPDC)
- Certified Deviation Investigation Expert (CDIE)
- Certified Process Deviation Auditor (CPDA)
- Certified Deviation Reporting Specialist (CDRS)
- Certified Deviation Control Officer (CDCO)
- Certified Process Deviation Consultant (CPDC)
- Certified Deviation Response Coordinator (CDRC)
- Certified Process Deviation Resolution Expert (CPDRE)
- Certified Deviation Reviewer (CDR)
- Certified Process Deviation Coordinator (CPDC)
- Certified Deviation Management Practitioner (CDMP)
- Certified Process Deviation Analyst (CPDA)
- Certified Deviation Root Cause Investigator (CDRCI)
- Certified Process Deviation Specialist (CPDS)
- Certified Deviation Handling Team Leader (CDHTL)
- Certified Process Deviation Compliance Officer (CPDCO)
Benefits Copied
Skills management software is important in process deviation handling to match skilled individuals with deviation identification, investigation, root cause analysis, corrective and preventive action (CAPA) management, and compliance auditing, improving deviation handling and regulatory compliance.
Author Copied
Revisions Copied
Tired of managing skills in Excel?
Say goodbye to Excel matrices. Start using AG5’s plug and play skill matrix software.
Recognized by G2 for Excellence in Skills Management
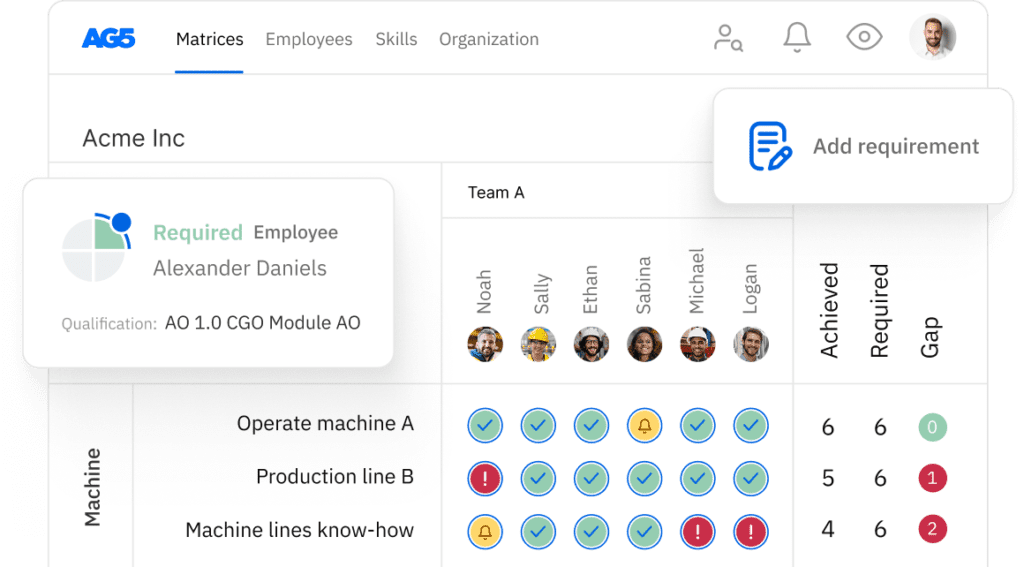