Industrial engineering skills matrix template
A skills matrix template is a tool that organizations can use to effectively manage and assess the industrial engineering skills and certification statuses of individual employees or teams.
Download your free template here
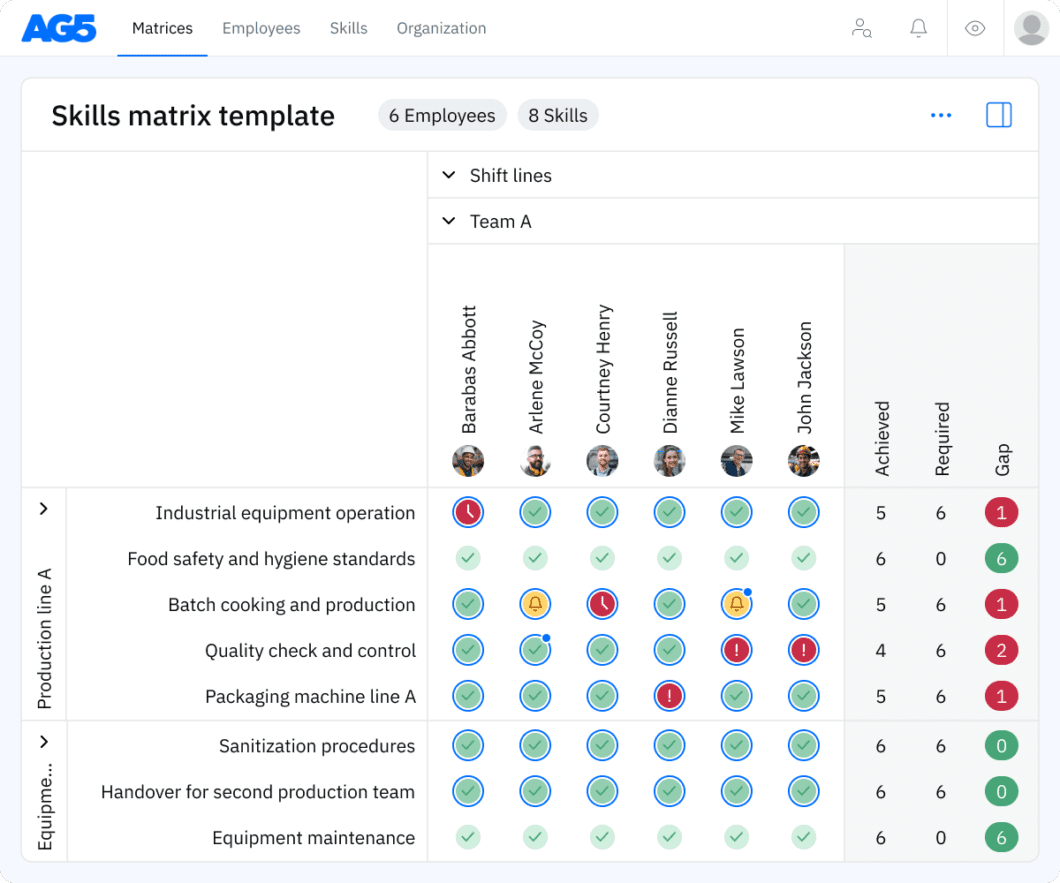
Overview Copied
A skills matrix template is a tool that organizations can use to effectively manage and assess the industrial engineering skills and certification statuses of individual employees or teams.
For example, you can use this industrial engineering skills matrix template to ensure that your teams have the right qualifications to implement and conduct rigorous quality control processes.
Production planning and scheduling
- Developing and managing production schedules to meet customer demands
- Using MRP (Material Requirements Planning) and ERP systems for production planning
- Balancing production workloads to optimize capacity utilization and minimize downtime
- Coordinating with procurement and inventory teams to ensure material availability
- Implementing Just-In-Time (JIT) production to minimize inventory levels and reduce lead times
Facility layout and design
- Designing optimal facility layouts to improve material flow and reduce waste
- Conducting space utilization studies to maximize efficiency in manufacturing areas
- Planning equipment and workstation placement for ergonomic and safety considerations
- Collaborating with cross-functional teams to ensure facility layout meets production requirements
- Implementing lean layout principles to minimize transportation and handling times
Process optimization and analysis
- Conducting time and motion studies to improve production efficiency
- Analyzing workflow to identify bottlenecks and recommend process improvements
- Implementing process mapping and value stream mapping to optimize operations
- Applying lean manufacturing techniques (e.g., 5S, Kaizen) to reduce waste
- Using simulation tools to model and test process improvements before implementation
Quality control and continuous improvement
- Developing and implementing quality control processes to ensure product standards are met
- Using Six Sigma methodologies (DMAIC) to reduce defects and improve quality
- Conducting root cause analysis (RCA) to identify and resolve quality issues
- Leading continuous improvement initiatives to enhance manufacturing processes
- Monitoring Statistical Process Control (SPC) data to ensure production consistency
Benefits Copied
Using a skills matrix template can benefit your industrial engineering teams in various ways.
- Optimized resource allocation. Assigning certified Six Sigma Black Belts to complex process improvement projects efficiently.
- Identifying skills gaps. Recognizing the need for additional training when engineers lack proficiency in emerging technologies like IoT.
- Succession planning. Ensuring smooth transitions by identifying potential successors for key roles within the production management team.
- Enhanced team collaboration. Facilitating effective cross-functional collaboration between quality engineers and manufacturing engineers for process optimization.
- Performance evaluation. Evaluating the performance of industrial engineers based on their demonstrated competencies in implementing lean manufacturing techniques.
Download the free Excel Industrial engineering skills matrix template Copied
We also have a free Excel template available that you can download if you are not ready to get started with AG5. To download it, please complete this form here.
Customizing a Industrial engineering skills matrix template Copied
The scope of a skills matrix can be as large or small as you choose. For example, it could cover your entire industrial engineering department – or only the process improvement team.
To customize a skills matrix to your needs, you should:
- Define focus. Clarify if the skills matrix pertains to an entire department or specific roles within it.
- Identify key skills. List essential competencies for each role or area of operation.
- Establish proficiency levels. Define skill proficiency levels, aligning them with job requirements.
- Set evaluation criteria. Create a clear evaluation process, considering on-the-job performance and training qualifications.
- Regularly review and update. Ensure regular reviews to adapt to evolving roles, technologies, and organizational goals.
Do you require a certification that is not included in the above list? No problem! You can easily add additional certifications yourself to customize the skills matrix to your organization’s needs.
You can also add your own employees and how they score against each certification. Not sure what scoring system to use? You can also add your own employees and how they score against each certification. Not sure what scoring system to use? Check out our “Ultimate guide to creating an Excel skills matrix.”
Looking for alternatives to Excel for your skills matrix template? Copied
AG5’s skills management software enables you to visualize and close skills gaps across your industrial engineering department or team – no need for complicated Excel spreadsheets. You’ll use intuitive skills matrices that bring together skills data and job requirements – and are always up to date.
Author Copied
Revisions Copied
Tired of managing skills in Excel?
Say goodbye to Excel matrices. Start using AG5’s plug and play skill matrix software.
Recognized by G2 for Excellence in Skills Management
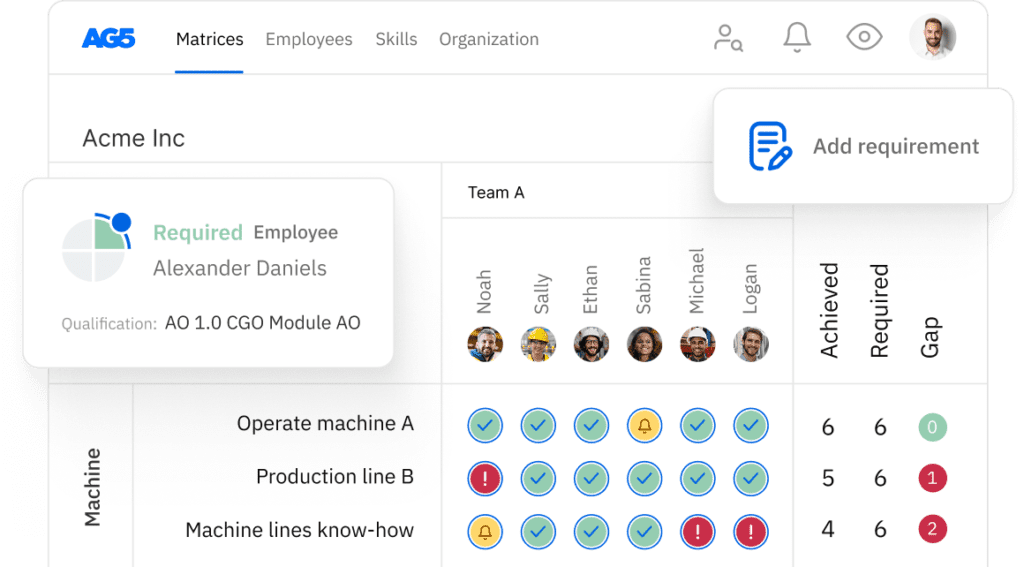