Closing the skills gap in modern assembly line operations
In this article, we’ll take a look at the skills gap in modern assembly line operations, factors that contribute to it and how a proper skills management strategy can help your organization.
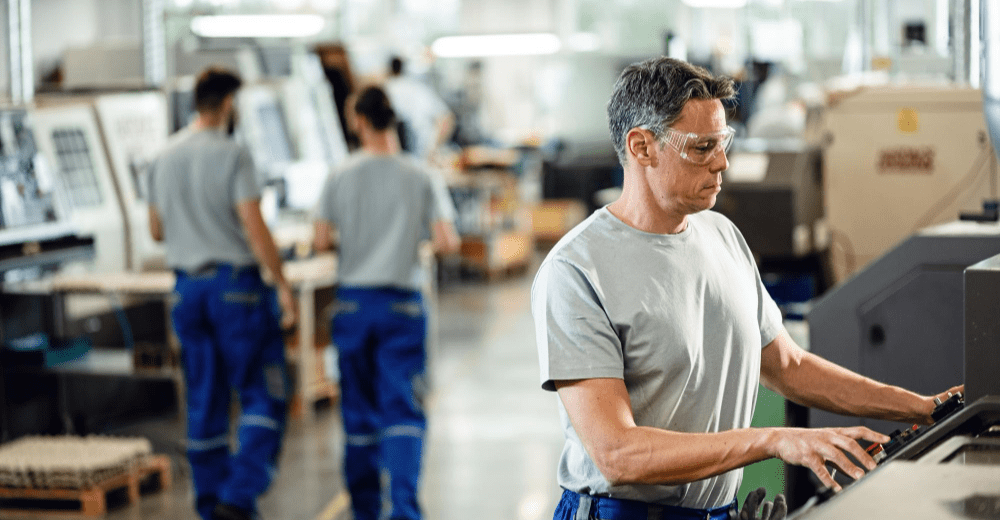
The rise of automation, AI, and other technologies in manufacturing environments is revolutionizing assembly line operations. This undoubtedly offers a great number of benefits to organizations – among them increased efficiency, reduced costs, and improved product quality. However, like any emerging technology, it also presents challenges, especially so in the potential widening skills gap that must be closed in order to keep operations running.
In this article, we’ll take a look at the skills gap in modern assembly line operations, factors that contribute to it, and how skills management software can help you take steps to close it.
The skills gap in modern assembly line operationsCopied
Research from Deloitte estimates that 2.1 million manufacturing jobs could go unfilled by 2030 due to the skills gap [1].
The consequences of so many unfilled jobs are dire, the research reveals, with organizations that do not take steps to close the skills gap reporting:
- Reduced productivity and efficiency. Workers struggling to operate automation systems efficiently can lead to production bottlenecks and increased cycle times, with 81% of organizations believing they will have trouble “maintaining production levels to satisfy customer demand.”
- Loss of revenue. Reduced productivity isn’t just frustrating – it negatively affects an organization’s bottom line. Here, 82% of organizations believe assembly line skills gaps will affect revenue growth.
- Competitive disadvantage. Companies that cannot adapt to modern assembly line requirements risk losing market share to competitors with a more skilled workforce. According to Deloitte’s research, 79% of manufacturing organizations believe the skills gap will negatively affect their ability to respond to new market opportunities.
What causes the skills gap in assembly line operations?Copied
In assembly line operations, the skills gap is the result of a cumulative effect of the several factors. Let’s take a look at three of the most pressing.
Rapid technological advancements
The greatest challenge with technological advancements on the assembly line involves the exponential pace in which it evolves, with data from Harvard Business Review [2] showing that:
29% of a job posting’s skills may not be needed the following year
This, of course, means that assembly line workers must be able to regularly adapt to new processes and systems. However, they must also possess the ability to frequently adapt. This is a skill within itself – one that must be taught and cultivated if an assembly line operation is to thrive.
An aging workforce
Many manufacturing organizations are grappling with an aging workforce, which currently comprises 25% of any given company’s total employees. Retirement, then, presents a major challenge – and has a great impact on the skills gap – on assembly lines or in other manufacturing environments.
In an article on the aging workforce in manufacturing, The Manufacturing Institute reveals that [3]:
- 90% of companies are “capitalizing on the talents and experiences of their older workers”
- 46% of those companies report “benefitting from older workers ‘to a great extent’”
Losing the knowledge, skills, and talent of veteran workers leaves a void that is difficult to fill with younger, less-experienced employees.
Lack of relevant or effective training programs
Traditional educational institutions often struggle to keep their curricula aligned with the latest technological advancements. They’re also largely ineffective, according HR industry publication HR Dive [4].
When trained in one-size-fits-all, “classroom-style” environments, the article states, employees forget:
- 50% of the presented information within an hour
- 70% within 24 hours
- and 90% within a week
This leaves employees ill-prepared for the realities of modern assembly line work, as the skills taught may not be retained – much less directly applicable – to the automated systems in use.
How to close assembly line skills gaps with skills management softwareCopied
The challenges listed above are complex and multifaceted, and as such require a strategic approach to surmount. To develop this approach, many manufacturing organizations are turning to skills management software.
Here, we’ll take a look at how manufacturing organizations are using such software to take significant steps towards addressing the challenges laid out in the previous section – ultimately helping them close skills gaps in modern assembly line operations.
Take a ‘dynamic’ approach to skills management
To avoid training employees for skills they do not – or will soon not – need, Harvard Business Review recommends leveraging “skills management as a dynamic exercise that embraces ambiguity, makes peace with imperfection, and frees up HR, managers, and employees to move fast in responding to the things they know and can anticipate.”
The article also states that:
- Organizations that adopt a dynamic approach to skills management report employees use 75% of the skills they learn.
Such an approach requires a full, clear oversight of the skills an organization’s employees possess and need – something the right skills management software will provide with easy-to-use dashboards that provide you with real-time information at a glance.
Develop personalized training programs
Personalized training programs work to address two of the challenges previously listed. For one, they are more effective at providing employees with the training they actually need – and are thus more likely to retain. Second, they help lessen he the impact of veteran employees leaving due to retirement.
Such programs – especially those related to upskilling, reskilling, and succession – are also what employees want, as they provide structured paths to acquire hands-on experience and knowledge that are more engaging and can often be accomplished on the job.
According to HR Dive:
- 91% of employees desire personalized training
- 90% want training that is “engaging and fun”
As skills management software provides you with an overview of your organization’s employees’ skills, you can use it to develop targeted training plans for individual employees. These plans can be based on what employees themselves want, what the organization needs, or a healthy mixture of both.
Build the right company culture
Without an engaged workforce, any skills management initiative will not be nearly as effective. This is particularly troubling in the manufacturing industry and on assembly lines, with research from Gallup revealing that [5]:
Only 25% of manufacturing workers are engaged in their roles
Skills management software offers several methods of approaching and rectifying these high levels of disengagement, especially considering several of Gallup’s proposed solutions: “allow for more control of work, create accountability, [and] communicate.”
The right software will provide access to employees on all levels of the organization – not just management. This means employees will have an active voice in their career’s progression, as well as a foundation on which transparent, open communication regarding that progression can take place. This will serve to boost workplace engagement – and help you develop skills management initiatives that provide the best possible results.
AG5 skills management software and assembly line operationsCopied
AG5’s skills management software can play a key role in your assembly line, providing you with the real-time data and analytics you need to effectively and efficiently track skills, develop training plans, and manage certifications and qualifications that your employees needs to keep operations running while staying safe and compliant.
Want to learn more? Schedule a free, live, 15-minute demo today to see how AG5’s skills management software holds the potential to transform the way your business operates.
Sources Copied
- Change view: Table
-
APA
# | Source title | Description | Publication | Retrieved | Source URL |
---|---|---|---|---|---|
1 | Creating pathways for tomorrow’s workforce today | Deloitte | - | April 29, 2024 | https://www2.deloitte.com/us/e.. |
2 | Organizations Need a Dynamic Approach to Teaching People New Skills | HBR | - | April 29, 2024 | https://hbr.org/2021/11/organi.. |
3 | The Aging of the Manufacturing Workforce | The manufacturing institute | - | April 29, 2024 | https://themanufacturinginstit.. |
4 | Why traditional classroom training isn’t enough for today’s employee | HR Drive | - | April 29, 2024 | https://www.hrdive.com/news/wh.. |
5 | 5 Keys to Boosting Workplace Culture in Manufacturing | Gallup | - | April 29, 2024 | https://news.gallup.com/busine.. |
Author Copied
Revisions Copied
New sources added.
Written by: Rick van Echtelt
Copy edited by: Adam Kohut