Die casting skills matrix template
A skills matrix template is a tool that organizations involved with die casting can use to effectively manage and assess the skills and knowledge of individual employees or teams.
Download your free template here
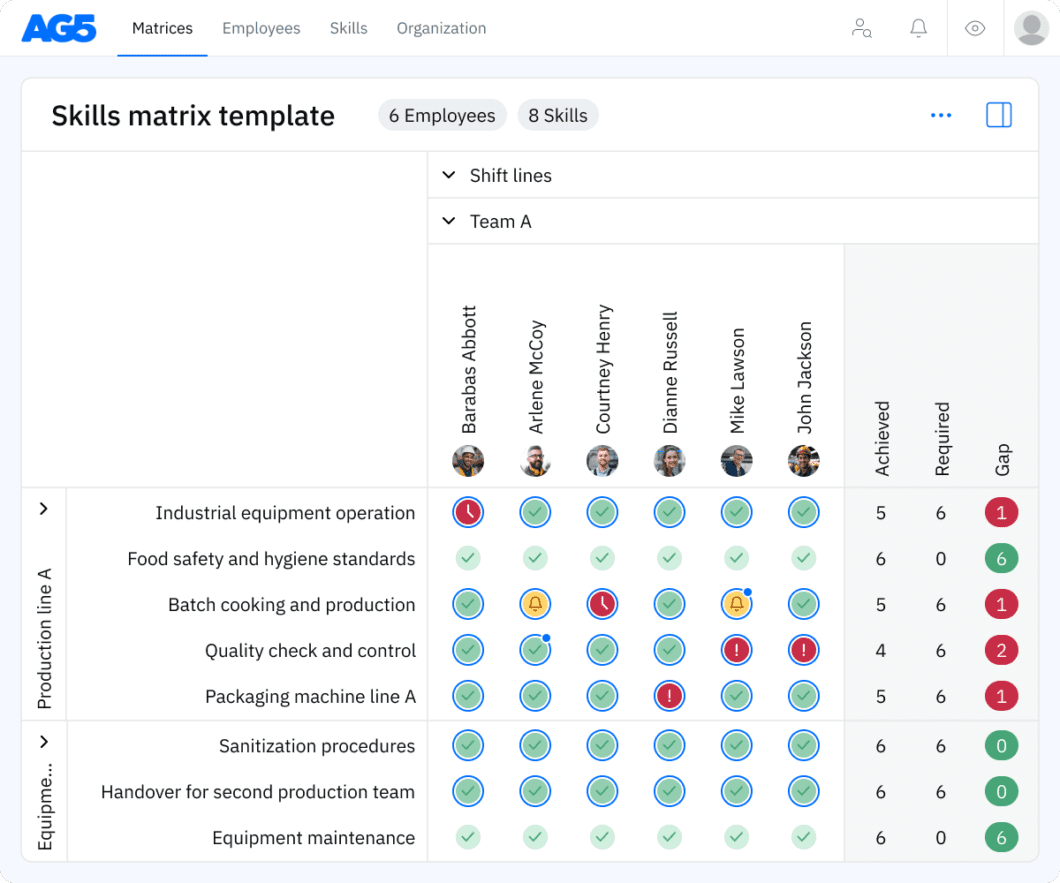
Overview Copied
A skills matrix template is a tool that organizations can use to effectively manage and assess the skills and certification statuses of individual employees or teams.
For example, you can use this skills matrix to monitor the certification statuses of your die casting technicians, ensuring compliance with industry standards and safety regulations.
Additionally, you could evaluate employees’ proficiency in quality management, resulting in improved product consistency, reduced defects, and enhanced customer satisfaction.
Die casting process operation
- Operation of die casting machines (e.g., hot-chamber, cold-chamber)
- Setup and changeover of die casting molds
- Adjusting machine parameters (e.g., temperature, pressure)
- Monitoring and controlling metal flow and solidification
- Troubleshooting casting defects
- Managing cycle times and production rates
- Die lubrication and cooling management
Mold and tooling maintenance
- Mold preparation and cleaning
- Inspection of molds for wear and damage
- Mold repairs and adjustments
- Preventive maintenance of casting molds
- Die coating and lubrication management
Quality control and inspection
- Inspecting cast parts for defects (e.g., porosity, shrinkage, cracks)
- Dimensional inspection of cast components
- Non-destructive testing of die-cast parts (e.g., X-ray, ultrasonic)
- Visual inspection and surface finish evaluation
- First-article inspection (FAI)
- Statistical Process Control (SPC) for die casting
Material handling and metallurgy
- Handling and melting of die-casting alloys (e.g., aluminum, zinc)
- Understanding of material properties (e.g., shrinkage rates, solidification)
- Alloy preparation and degassing techniques
- Metal pouring and gating system design
- Managing impurities and ensuring material quality
Machine maintenance and troubleshooting
- Preventive maintenance of die casting machines
- Troubleshooting machine malfunctions
- Hydraulic and pneumatic system maintenance
- Calibration and adjustment of die casting equipment
- Robot and automation integration and maintenance
Benefits Copied
Using a skills matrix template can benefit your die casting operations in various ways. Among them:
- Enhanced product consistency. By utilizing a skills matrix, you can ensure that employees with the appropriate expertise are assigned to specific tasks, leading to consistent product quality and uniformity in the die casting process.
- Reduced defects and rework. Properly assessing employee skills through a skills matrix helps in assigning the right personnel for critical tasks, reducing the likelihood of errors and the need for costly rework in die casting operations.
- Increased operational safety. By accurately evaluating employees’ competencies, you can ensure that workers are appropriately trained for handling the machinery and materials involved in the die casting process, thereby reducing the risk of accidents and promoting a safer work environment.
- Optimized machine utilization. Effectively managing employee skills through the skills matrix enables better utilization of the die casting machinery, as tasks can be assigned to the most competent personnel, maximizing the efficiency and output of the machines.
- Cost reduction. A well-managed skills matrix can lead to optimized resource allocation and improved production processes, ultimately reducing overall production costs and enhancing the profitability of die casting operations.
Download the free Excel Die casting skills matrix template Copied
We also have a free Excel template available that you can download if you are not ready to get started with AG5. To download it, please complete this form here.
Author Copied
Revisions Copied
Tired of managing skills in Excel?
Say goodbye to Excel matrices. Start using AG5’s plug and play skill matrix software.
Recognized by G2 for Excellence in Skills Management
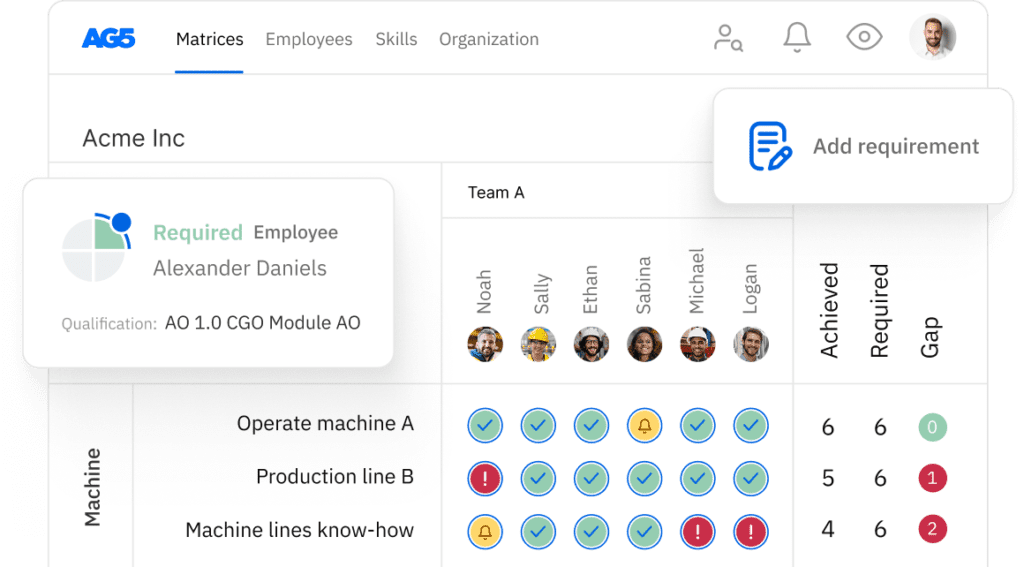