The Future of Manufacturing: Industry 4.0
In this article we discuss Industry 4.0 manufacturing. It explores the transformative impact of Industry 4.0 technologies on manufacturing processes, emphasizing automation, data exchange, and digital technologies’ integration.
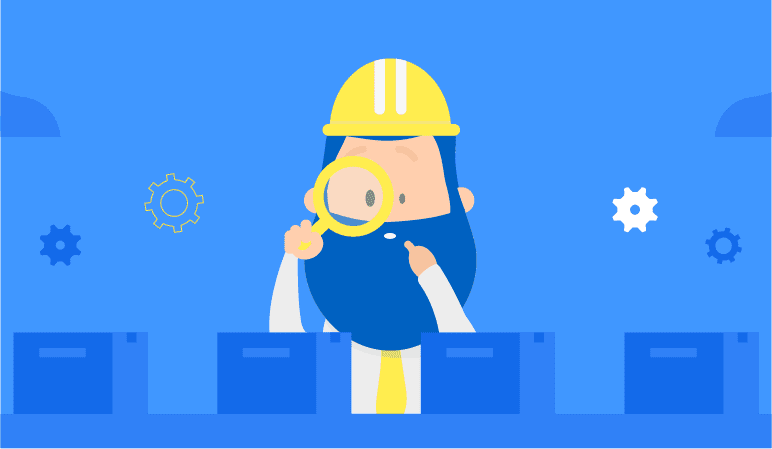
Manufacturing is changing, fast. Innovation – the advancement of smart manufacturing and digital technologies, specifically – is driving us into the fourth industrial revolution: Industry 4.0.
Much as the three previous industrial overhauls, Industry 4.0 will not, and is not an overnight revolution: it is gradual but definite. Many companies have already enhanced their processes with smart and autonomous systems and as more follow suit, the momentum of revolution quickens. Adding fuel to the fire is the tech itself: advancements are coming along in leaps and bounds, making products more intelligent, more affordable, and more readily available – further spurring manufacturing to Industry 4.0. Exciting, hey!
So, what does this mean for you?Copied
Your business will likely change. As the industry becomes more embedded with smarter and more communicative computers, which have advanced way beyond basic mining of data. There is now plenty of equipment to help utilise this data to make businesses more efficient, resourceful, and productive. An added benefit of this is that it can help to reduce waste throughout the whole supply chain, driving industries to a more sustainable future.
Manufacturing is one industry already reaping the rewards of Industry 4.0, as smart factories with connected machines and intelligent robots are already common practice for many firms. Being as this the second digital industrial revolution, digital transformation is no longer a novel topic in boardrooms. A strong infrastructure for technological advancements is already in place, so the questions now are: how do we make our processes smarter? And, how do we ensure our workforce continues to perform optimally?
How do we make manufacturing processes smarter?
The initial “smarting” of factories is often by fitting automated maintenance sensors to the production process which detect exactly where faults occur. The findings will then be put together quickly and automatically into comprehensive and easy-to-read reports. What an invaluable tool for optimisation! Companies which have installed such devices continually report increases to capital yield. It should be noted though that these smart features are not entirely self-sufficient though, as they require human comprehension. Making sure that your workforce knows how to use these new tools properly then is of paramount importance. Which is where decisions for reskilling or upskilling will come into play.
How well does your manufacturing company perform in Industry 4.0?
The final key element of Industry 4.0 in manufacturing is the introduction of robotics and autonomous machinery. Taking shape in many forms and sizes, manufacturers are taking advantage of advancements in the field of robotics to bolster productivity and to save costs. Whether that is in the automotive industry where robotics cut and welding car parts, or in the service industry where robotics are being introduced for basic customer interactions. Robotics are everywhere. Again, much as with smart factories, there is still a great degree of human oversight that needs to present. Which is why many are dubbing these robotic features with the more apt name: “co-botics”. The skill level of workforce in managing these emerging industry 4.0 technologies will play a huge part in how well your manufacturing company performs. So make sure you are prepared.
Copied
Data. So much data!Copied
Industry 4.0 will also impact the way we understand and conceptualise manufacturing. This can only mean one thing: more data!
How this increase in data is handled and protected is an issue at the forefront of minds throughout the industry. There does seem to be a common consensus that the tools employed need to be user-friendly, centralised, and highly secure. In one report, Gerard Bartley, Global Master Data Manager at Jacobs Douwe Egberts, who, notably, uses Ag5 for their skills management software, explained that:
“Data management and data governance are critical, and without these firmly in place, business data is often difficult to use and expensive to maintain. It’s important to tame your data sources and get real value out of them.”
As the industry evolves and the technology advances, it is imperative that your staff keeps up. New and improved equipment means new qualifications, new skills, and new standards. It is crucial then to have a clear and structured roadmap in place for tomorrow and to know exactly how qualified and how skilled your current staff are. Training will need to become a central activity in your organisation!
Training comes in many forms; however, falls into two distinctive categories: upskilling and reskilling. The former is when you improve skills and knowledge in the role which is already performed. While the latter involves learning new skills for a new task. This, of course, means more data! Qualifications and skill levels need to be recorded and stored in an easily accessible place. Centralising it, then, is a good idea, as it allows for information to be collected, logged, and used as and when is needed. It also eradicates the mess of multiple spreadsheets across different departments. And now with the speed of development and the necessity to ensure that staff remain at the height of their game, centralising data and eradicating silos is more important than ever. “Do not feed the data monster! Control it!”
How AG5 can help manufacturing ease into Industry 4.0Copied
AG5 helps clients visualize and close their skills gaps with skills management software for manufacturers. But how? By clearly mapping their workforce’s current skills, and tracking progress against business requirements to get their organization ready for the future and stay compliant
With AG5 Skills Management Software you can create clear cross-company skills matrices and dashboards within a centralised skills hub, integrating data from other HR and learning tools. Moving away from unmanageable spreadsheets, AG5 provides clear, concise, and audit-proof skills matrices that make workforce management easy and convenient.
By opting for AG5 Skills Management Software, you will always find yourself ready for any advancements and developments within your organisation. You will also be able to identify current skills gaps quickly and easily, and also those which may arise in the future. This not only ensures business continuity but also helps you stay ahead of the game in the ever-evolving industry.
Find out how AG5 can help you prepare for Industry 4.0 or schedule a live demo