How to make the most of capacity management
During this article we delve into maximizing capacity management. We examine the significance of efficient workforce capacity handling and presents tactics for enhancing organizational productivity and performance.
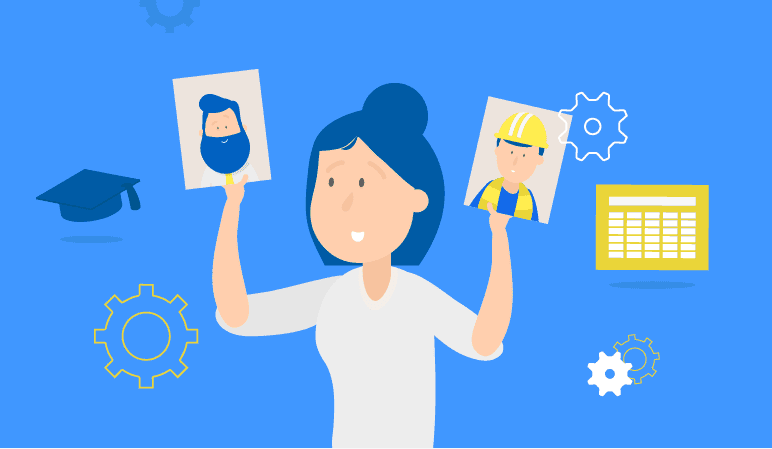
Striking the right balance between workloads and staffing levels is an important factor for managing operational processes effectively and efficiently. Capacity management can help. But what is capacity management exactly? And how can you implement it successfully?
But what is capacity management?Copied
Capacity management is a key component of workforce management. We use the term to refer to structurally aligning and managing workloads and staff availability. It precedes generating daily or weekly work schedules. And it’s more than just short-term planning – it focuses primarily on the longer term. What’s more, it comprises two dimensions – a quantitative (how many staff members you have available) and a qualitative (how skilled these staff members are and their suitability for a certain task or role).
Based on historical data and patterns, you can forecast upcoming workloads and staff availability. For most organizations, these never remain constant throughout the year.
- Factors that can cause fluctuations include repeat production runs in a certain month or staff off sick during flu season.
- On the personnel front, you also need to examine how many FTEs you have in each department and on which days they work, when they have vacations planned, and who is off sick.
Capacity management provides an answer to the all-important question – does my organization have enough qualified employees to meet internal and external customer demand to the required level? Not only now, but across all peaks and troughs to come. Capacity planners constantly analyze a variety of scenarios that could affect workloads and staff availability. Many of the questions they ask themselves start with ‘What if … ?’
Why even bother with capacity management?Copied
There are simply too many benefits to be gained by applying capacity management properly and consistently. It helps you:
- respond effectively and efficiently to future requirements – you know who you have available in-house to tackle an urgent project, for example is your junior software developer capable of handling the job and, if so, can you keep your senior developer available for other more complex assignments?
- avoid customer disappointment and/or overworked staff – you know exactly what output levels you can achieve with the staffing levels available to you.
- visualize your workforce’s skills, competences, and qualifications – you know exactly who can do what and who can’t.
- spot skills gaps sooner – you know before committing to a big data project whether or not you actually have a shortage of qualified data analysts.
- manage and control costs – you know exactly what costs you’ll be incurring in terms of both production and personnel.
- plan staffing levels for peak periods – you know when to ramp up staffing levels to meet peak seasonal demand, for example the production of outdoor articles or items as the summer approaches.
4 steps to effective capacity managementCopied
But how should you implement capacity management in practice? Read on to find out more about the basics of capacity planning.
1. Analyze
Capacity management starts with a thorough analysis of your current situation. Examine your workload (current and expected) and staff availability from one or more of the angles detailed below:
- convert ‘production indicators’ (turnover, invoices, inbound/outbound calls, meetings …) to work hours to get a better idea of the actual workload
- measure how long it takes to perform certain tasks to determine just how labor intensive processes can be
- determine throughput times for each activity and each employee to help correlate workloads to staffing levels
- benchmark your processes so you can compare your organization with others in your sector
- identify the bottlenecks or weak links in your operational processes, for example when do you need to work overtime?
Next, sort work activities into one of the three following categories:
- Direct, time-bound activities that repeat on a daily basis – record how many people you need and the skills they need on an hour-by-hour basis
- Non-time-related activities, for example archiving, toolbox meetings, and other incidental tasks and events
- Unplanned/unforeseen activities – estimate the staffing levels required to deal with these based on historical data
To determine the capacity you need, calculate a gross-net ratio and your gross capacity based on all your employment contracts (full- and part-time).
Next, deduct the total direct non-worked hours, for example sick leave, vacation days, special leave, and indirect non-worked hours, for example training, learning, maintenance, to determine your net capacity.
Lastly, plan for unforeseen eventualities by creating reserve capacity in the form of an external (or internal) flex pool.
2. Align
Once you’ve performed a thorough analysis, it’s time to align your workload and staffing levels to find the best balance.
To do this, you need to answer two main questions:
- Is my current capacity sufficient to tackle all incoming work?
- How am I going to plan and assign this available capacity?
It’s important to approach these questions from as wide an angle as possible. Don’t just look at quantitative data, but take corporate culture, quality standards, and terms of employment into consideration, too.
3. Plan
Slowly but surely, things should now be getting a little clearer. Draft a capacity plan and start assigning your personnel capacity to specific tasks and timelines.
Don’t forget to take account of seasonal fluctuations in capacity requirements and which strategies you want to adopt, as well as the contingency plans to deal with sick leave, market changes, increasing demand for flex workers …
4. Review
Creating a capacity plan isn’t a one-off event. It should be a living, breathing plan that adapts to ever-changing circumstances, so keep reviewing and adjusting as needed.
Now more than ever, the balance between demand and supply can shift extremely fast and before you know it you’ll find a huge discrepancy between reality and what you’ve gotten written down on paper. If workloads are increasing, it’s important to determine whether this is a one-off/temporary situation or a question of structural growth.
Tip – use skills management software!Copied
The success of your capacity management efforts depends to a large extent on having a clear picture of your workforce’s skills, competences, and qualifications. But what’s the best way to paint this picture? Consider using skills management software! AG5’s software allows you to record, save, and manage all your staff’s skills, competences, and qualifications to the cloud.
- Put together teams based on relevant skills
- Find temporary or permanent replacements quickly and easily
- Spot and close skills gaps
- Create a skilled and qualified flex pool
Using skills management software, all this and more is possible. Time to take your capacity management to the next level?
Find out how AG5’s skills management software works or schedule a live demo!