Solving manufacturing workforce challenges amid global disruption
Learn how workforce and skills management can provide you with better visibility into skills, smarter scheduling, and clear training paths – so you can navigate labor shortages, compliance issues, and trade-related disruptions.
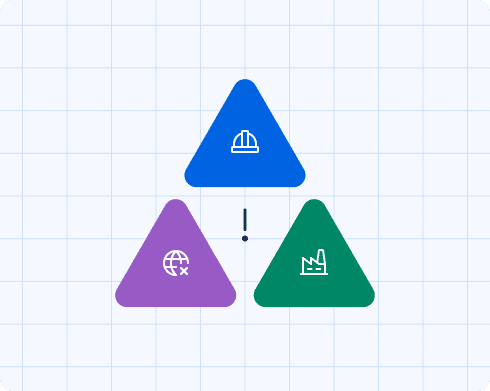
The manufacturing sector is under pressure. Labor shortages, supply chain issues, and compliance-related challenges are nothing new, but ongoing tariff wars, reshoring strategies, and global disruption have raised the stakes [1].
To keep up, manufacturers need people with the right skills, in the right roles, at the right time, backed by smart workforce planning. That’s where the combination of AG5 and UKG comes into play.
Together, AG5 and UKG help manufacturers manage who is working, as well as what those workers are qualified to do. UKG handles the workforce side – shifts, schedules, payroll, and HR – while AG5 tracks skills, training, and compliance. When integrated, they offer operations and HR leaders a holistic view of workforce readiness.
The manufacturing workforce challengeCopied
Manufacturers are currently facing a deepening labor crisis, with more than 2 million jobs that may unfilled by 2030 in the US due to skills gaps and demographic changes [2]. That’s a massive risk for productivity and growth.
Simultaneously, the workplace itself is changing. According to McKinsey, manufacturers are dealing with multiple waves of disruption: automation, evolving job roles, and the reshoring of operations due to geopolitical tensions [3]. With production coming back home in many regions, labor demand is increasing, but the skilled labor to match it isn’t always there.
As companies adjust processes or expand into new markets, they must also stay compliant with evolving safety rules, labor laws, and industry standards. Failing to track workforce certifications or mandatory training can lead to fines or unsafe workplaces.
These challenges are connected, and manufacturers need a way to respond in a connected way. That’s why a combined workforce and skills management solution matters.
Copied
5 ways to tackle the manufacturing workforce challengeCopied
Growing skill gaps and sudden geopolitical shifts demand practical responses from manufacturing organizations. Here are five steps you can take to better manage risk, remain compliant, and build a resilient workforce.
Match skills to roles
Make sure employees have the right skills for the work they do. Use clear role-based skill profiles and regularly assess where skill gaps exist. Employees who believe that their job matches their skills are more likely to be engaged – and therefore remain in their roles longer. They will also be more productive [4].
Track compliance automatically
Stay on top of required training, certifications, and safety standards. Automating this process reduces the risk of failing audits or exposing workers to unsafe conditions. A structured system can flag missing qualifications before they become a problem.
Use data when hiring
Look beyond resumes. Analyze your current workforce data to understand what skills you already have, as well as what you’re missing. This helps HR and hiring managers make better, faster decisions based on real needs.
Make skills visible
Build a centralized overview of workforce skills, training history, and future needs. This makes planning easier and helps managers respond quickly when regulations or production needs change.
Plan for change
The industry won’t stand still. Manufacturers need agile workforce strategies to keep up with digital transformation – which requires employees equipped with digital skills – as well as automation and shifting market demands [5]. Regular reviews and scenario planning can help your teams stay ready.
UKG’s role: Workforce management & HRCopied
UKG helps manufacturers take control of workforce operations, especially in volatile conditions. It supports HR and operations teams with tools for:
- Optimizing staffing and shift planning. When demand shifts overnight, UKG helps reassign staff quickly without causing coverage gaps
- Managing compliance at the HR level. UKG handles time tracking, payroll, and labor regulations, so you’re less likely to miss compliance requirements
- Improving the frontline worker experience. By automating routine scheduling and time-off tasks, UKG gives workers more control and reduces admin overhead
- Adapting to production changes. As manufacturers shift facilities due to tariffs or supply issues, UKG supports agile workforce deployment
UKG makes HR easier, and helps manufacturers stay productive when the labor situation is anything but stable. For instance, during a reshoring effort, a company might need to quickly onboard a large number of employees. UKG helps manage hiring, shift planning, and payroll setup in a coordinated way.
AG5’s role: Skills management & complianceCopied
Manufacturers need workers on the floor, but those workers must be certified, trained, and ready for their specific roles. This means you will need to keep track of these qualifications in addition to employees themselves.
AG5 gives manufacturing leaders:
- A live view of workforce skills. Managers can see at a glance who is certified to run which machines, who is overdue for training, and who is ready to step into new roles
- Automated compliance tracking. AG5 tracks training expiration dates, audit readiness, and safety requirements in real time
- Support for quick redeployment. When operations shift due to tariffs or local demand, AG5 shows which workers can step into new roles, or where upskilling is quickly needed
- A faster way to close skills gaps. Instead of reacting after an issue, AG5 helps identify and fill skills shortages before they affect production or business operations
AG5 is especially helpful when regulations change or production lines shift rapidly. For example, if a company moves production from one region to another, AG5 ensures the right skills and certifications are in place before the first shift begins.
Copied
How UKG & AG5 work togetherCopied
UKG and AG5 each cover a key part of the workforce equation, together offering a holistic solution. By integrating the platforms, manufacturers can align HR, operations, and training.
For example:
- UKG identifies when more staff are needed
- AG5 identifies which staff have the right skills and certifications
- Together, they ensure the shift is covered and compliant
This approach is especially useful during global disruption. If a tariff change makes it more economical to produce locally, companies can shift operations and rely on UKG and AG5 to adjust staffing, track skills, and ensure training, all without starting from scratch.
While the challenges that manufacturers face may not dissipate anytime soon, the right tools can help, and can make the difference between organizations who do and do not succeed.
UKG brings clarity and AG5 brings skills visibility. Together, they help manufacturers stay ready, even in the face of disruption. For HR, operations, and training leaders, that means fewer surprises and smoother transitions, whether you’re moving production, ramping up new teams, or quickly closing crucial skills gaps in highly technical roles.
Ready to see how AG5 and UKG combine to make sure manufacturing organizations have employees are where they need to be and ready for work? Schedule a free, live, 15-minute demo today for a custom look.
Sources Copied
- Change view: Table
-
APA
# | Source title | Description | Publication | Retrieved | Source URL |
---|---|---|---|---|---|
1 | HR, workforce, and payroll solutions to improve productivity, empower talent, and boost engagement | UKG | July 1, 2024 | July 1, 2025 | https://www.ukg.com/industry-s.. |
2 | 2.1 Million Manufacturing Jobs Could Go Unfilled by 2030 | Workforce News | May 4, 2021 | July 1, 2025 | https://themanufacturinginstit.. |
3 | Investing in productivity growth | McKinsey | March 27, 2024 | July 1, 2025 | https://www.mckinsey.com/mgi/o.. |
4 | State of the Global Workplace | Gallup | June 1, 2025 | July 1, 2025 | https://www.gallup.com/workpla.. |
5 | 2025 Manufacturing Industry Outlook | Deloitte | November 20, 2024 | July 1, 2025 | https://www.deloitte.com/us/en.. |